අර්ධ සන්නායක නිෂ්පාදන ක්රියාවලියේ තීරණාත්මක පියවරක් ලෙස වේෆර් ඩයිසිං තාක්ෂණය, චිප ක්රියාකාරිත්වය, අස්වැන්න සහ නිෂ්පාදන පිරිවැය සමඟ සෘජුවම සම්බන්ධ වේ.
#01 වේෆර් ඩයිසිං වල පසුබිම සහ වැදගත්කම
1.1 වේෆර් ඩයිසිං අර්ථ දැක්වීම
වේෆර් ඩයිසිං (ස්ක්රයිබිං ලෙසද හැඳින්වේ) අර්ධ සන්නායක නිෂ්පාදනයේ අත්යවශ්ය පියවරක් වන අතර, සැකසූ වේෆර් බහු තනි ඩයි වලට බෙදීම අරමුණු කර ගෙන ඇත. මෙම ඩයිස් සාමාන්යයෙන් සම්පූර්ණ පරිපථ ක්රියාකාරිත්වය අඩංගු වන අතර ඉලෙක්ට්රොනික උපාංග නිෂ්පාදනයේදී අවසානයේ භාවිතා වන මූලික සංරචක වේ. චිප සැලසුම් වඩාත් සංකීර්ණ වන අතර මානයන් අඛණ්ඩව හැකිලෙන විට, වේෆර් ඩයිසිං තාක්ෂණය සඳහා නිරවද්යතාවය සහ කාර්යක්ෂමතා අවශ්යතා වඩ වඩාත් දැඩි වෙමින් පවතී.
ප්රායෝගික මෙහෙයුම් වලදී, වේෆර් ඩයිසිං සාමාන්යයෙන් දියමන්ති තල වැනි ඉහළ නිරවද්ය මෙවලම් භාවිතා කර එක් එක් ඩයි එක නොවෙනස්ව පවතින බව සහ සම්පූර්ණයෙන්ම ක්රියාකාරී බව සහතික කරයි. ප්රධාන පියවර අතරට කැපීමට පෙර සූදානම් වීම, කැපීමේ ක්රියාවලියේදී නිරවද්ය පාලනය සහ කැපීමෙන් පසු තත්ත්ව පරීක්ෂාව ඇතුළත් වේ.
කැපීමට පෙර, නිවැරදි කැපුම් මාර්ග සහතික කිරීම සඳහා වේෆරය සලකුණු කර ස්ථානගත කළ යුතුය. කැපීම අතරතුර, වේෆරයට හානි වීම වැළැක්වීම සඳහා මෙවලම් පීඩනය සහ වේගය වැනි පරාමිතීන් දැඩි ලෙස පාලනය කළ යුතුය. කැපීමෙන් පසු, සෑම චිපයක්ම කාර්ය සාධන ප්රමිතීන් සපුරාලන බව සහතික කිරීම සඳහා පුළුල් තත්ත්ව පරීක්ෂණ පවත්වනු ලැබේ.
වේෆර් ඩයිසිං තාක්ෂණයේ මූලික මූලධර්මවලට කැපුම් උපකරණ තෝරා ගැනීම සහ ක්රියාවලි පරාමිතීන් සැකසීම පමණක් නොව, කැපීමේ ගුණාත්මකභාවය කෙරෙහි ද්රව්යවල යාන්ත්රික ගුණාංග සහ ලක්ෂණවල බලපෑම ද ඇතුළත් වේ. නිදසුනක් ලෙස, අඩු-k ඩයෙලෙක්ටික් සිලිකන් වේෆර්, ඒවායේ බාල යාන්ත්රික ගුණාංග නිසා, කැපීමේදී ආතති සාන්ද්රණයට බෙහෙවින් ගොදුරු වන අතර, එය චිපින් සහ ඉරිතැලීම් වැනි අසාර්ථකත්වයන්ට මග පාදයි. අඩු-k ද්රව්යවල අඩු දෘඪතාව සහ බිඳෙනසුලු බව නිසා, විශේෂයෙන් කැපීමේදී යාන්ත්රික බලය හෝ තාප ආතතිය යටතේ ව්යුහාත්මක හානිවලට ඒවා වැඩි ප්රවණතාවක් ඇති කරයි. මෙවලම සහ වේෆර් මතුපිට අතර සම්බන්ධතාවය, ඉහළ උෂ්ණත්වයන් සමඟ සම්බන්ධ වීමෙන්, ආතති සාන්ද්රණය තවදුරටත් උග්ර කළ හැකිය.
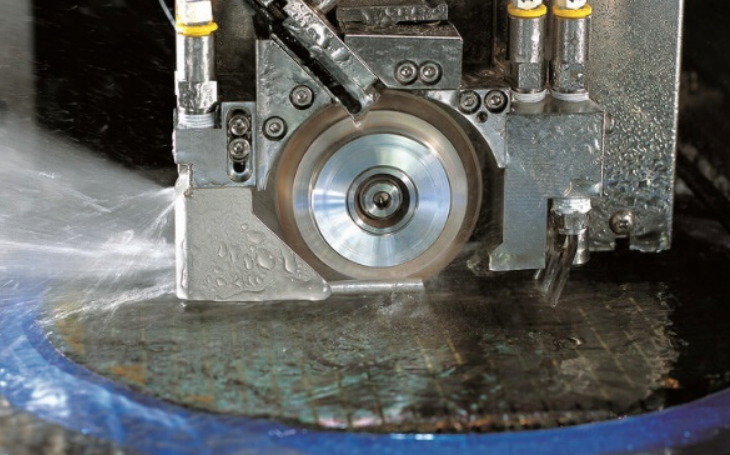
ද්රව්ය විද්යාවේ දියුණුවත් සමඟ, වේෆර් ඩයිසිං තාක්ෂණය සාම්ප්රදායික සිලිකන් පාදක අර්ධ සන්නායකවලින් ඔබ්බට ගැලියම් නයිට්රයිඩ් (GaN) වැනි නව ද්රව්ය ඇතුළත් කර ඇත. මෙම නව ද්රව්ය, ඒවායේ දෘඪතාව සහ ව්යුහාත්මක ගුණාංග නිසා, ඩයිසිං ක්රියාවලීන් සඳහා නව අභියෝග මතු කරන අතර, කැපුම් මෙවලම් සහ ශිල්පීය ක්රමවල තවදුරටත් වැඩිදියුණු කිරීම් අවශ්ය වේ.
අර්ධ සන්නායක කර්මාන්තයේ තීරණාත්මක ක්රියාවලියක් ලෙස, අනාගත ක්ෂුද්ර ඉලෙක්ට්රොනික විද්යාව සහ ඒකාබද්ධ පරිපථ තාක්ෂණයන් සඳහා අඩිතාලම දමමින්, පරිණාමය වන ඉල්ලුමට සහ තාක්ෂණික දියුණුවට ප්රතිචාර වශයෙන් වේෆර් ඩයිසිං අඛණ්ඩව ප්රශස්තකරණය කෙරේ.
වේෆර් ඩයිසිං තාක්ෂණයේ වැඩිදියුණු කිරීම් සහායක ද්රව්ය සහ මෙවලම් සංවර්ධනයෙන් ඔබ්බට යයි. ඒවාට ක්රියාවලි ප්රශස්තිකරණය, උපකරණ ක්රියාකාරිත්වයේ වැඩිදියුණු කිරීම් සහ ඩයිසිං පරාමිතීන්ගේ නිරවද්ය පාලනය ද ඇතුළත් වේ. මෙම දියුණුව මඟින් වේෆර් ඩයිසිං ක්රියාවලියේ ඉහළ නිරවද්යතාවය, කාර්යක්ෂමතාව සහ ස්ථාවරත්වය සහතික කිරීම, අර්ධ සන්නායක කර්මාන්තයේ කුඩා මානයන්, ඉහළ ඒකාබද්ධතාවය සහ වඩාත් සංකීර්ණ චිප ව්යුහයන් සඳහා වන අවශ්යතාවය සපුරාලීම අරමුණු කරයි.
සංවර්ධන ප්රදේශය | නිශ්චිත පියවර | බලපෑම් |
ක්රියාවලි ප්රශස්තිකරණය | - වඩාත් නිවැරදි වේෆර් ස්ථානගත කිරීම සහ මාර්ග සැලසුම් කිරීම වැනි මූලික සූදානම වැඩි දියුණු කිරීම. | - කැපුම් දෝෂ අඩු කර ස්ථාවරත්වය වැඩි දියුණු කරන්න. |
- කැපුම් දෝෂ අවම කර ස්ථාවරත්වය වැඩි දියුණු කරන්න. | - මෙවලම් පීඩනය, වේගය සහ උෂ්ණත්වය සකස් කිරීම සඳහා තත්ය කාලීන අධීක්ෂණ සහ ප්රතිපෝෂණ යාන්ත්රණයන් අනුගමනය කරන්න. | |
- වේෆර් කැඩී යාමේ අනුපාත අඩු කර චිපයේ ගුණාත්මකභාවය වැඩි දියුණු කරන්න. | ||
උපකරණ කාර්ය සාධනය වැඩි දියුණු කිරීම | - ඉහළ නිරවද්යතාවයකින් යුත් යාන්ත්රික පද්ධති සහ උසස් ස්වයංක්රීය පාලන තාක්ෂණය භාවිතා කරන්න. | - කැපීමේ නිරවද්යතාවය වැඩි දියුණු කිරීම සහ ද්රව්ය නාස්තිය අඩු කිරීම. |
- ඉහළ දෘඪතාවක් සහිත ද්රව්ය වේෆර් සඳහා සුදුසු ලේසර් කැපුම් තාක්ෂණය හඳුන්වා දීම. | - නිෂ්පාදන කාර්යක්ෂමතාව වැඩි දියුණු කිරීම සහ අතින් දෝෂ අඩු කිරීම. | |
- ස්වයංක්රීය අධීක්ෂණය සහ ගැලපීම් සඳහා උපකරණ ස්වයංක්රීයකරණය වැඩි කිරීම. | ||
නිරවද්ය පරාමිති පාලනය | - කැපුම් ගැඹුර, වේගය, මෙවලම් වර්ගය සහ සිසිලන ක්රම වැනි පරාමිතීන් සියුම් ලෙස සකසන්න. | - ඩයි අඛණ්ඩතාව සහ විදුලි ක්රියාකාරිත්වය සහතික කිරීම. |
- වේෆර් ද්රව්ය, ඝණකම සහ ව්යුහය මත පදනම්ව පරාමිතීන් අභිරුචිකරණය කරන්න. | - අස්වැන්න අනුපාත ඉහළ නැංවීම, ද්රව්ය නාස්තිය අඩු කිරීම සහ නිෂ්පාදන පිරිවැය අඩු කිරීම. | |
උපායමාර්ගික වැදගත්කම | - වෙළඳපල ඉල්ලුම සපුරාලීම සඳහා නව තාක්ෂණික මාර්ග අඛණ්ඩව ගවේෂණය කිරීම, ක්රියාවලීන් ප්රශස්ත කිරීම සහ උපකරණ හැකියාවන් වැඩි දියුණු කිරීම. | - චිප් නිෂ්පාදන අස්වැන්න සහ කාර්ය සාධනය වැඩි දියුණු කිරීම, නව ද්රව්ය සහ උසස් චිප් නිර්මාණ සංවර්ධනයට සහාය වීම. |
1.2 වේෆර් ඩයිසිං වල වැදගත්කම
අර්ධ සන්නායක නිෂ්පාදන ක්රියාවලියේදී වේෆර් ඩයිසිං තීරණාත්මක කාර්යභාරයක් ඉටු කරන අතර එය පසුකාලීන පියවරයන්ට මෙන්ම අවසාන නිෂ්පාදනයේ ගුණාත්මකභාවය සහ ක්රියාකාරිත්වයට සෘජුවම බලපායි. එහි වැදගත්කම පහත පරිදි විස්තර කළ හැකිය:
පළමුව, කැට කැපීමේ නිරවද්යතාවය සහ අනුකූලතාව චිප් අස්වැන්න සහ විශ්වසනීයත්වය සහතික කිරීම සඳහා යතුරයි. නිෂ්පාදනය අතරතුර, වේෆර් සංකීර්ණ පරිපථ ව්යුහයන් රාශියක් සෑදීම සඳහා බහු සැකසුම් පියවරයන්ට භාජනය වන අතර, ඒවා නිශ්චිතවම තනි චිප් (ඩයිස්) ලෙස බෙදිය යුතුය. කැට කැපීමේ ක්රියාවලියේදී පෙළගැස්වීමේදී හෝ කැපීමේදී සැලකිය යුතු දෝෂ තිබේ නම්, පරිපථවලට හානි සිදුවිය හැකි අතර එය චිපයේ ක්රියාකාරීත්වයට සහ විශ්වසනීයත්වයට බලපායි. එබැවින්, ඉහළ නිරවද්ය කැට කැපීමේ තාක්ෂණය එක් එක් චිපයේ අඛණ්ඩතාව සහතික කරනවා පමණක් නොව, අභ්යන්තර පරිපථවලට හානි වීම වළක්වයි, සමස්ත අස්වැන්න අනුපාතය වැඩි දියුණු කරයි.
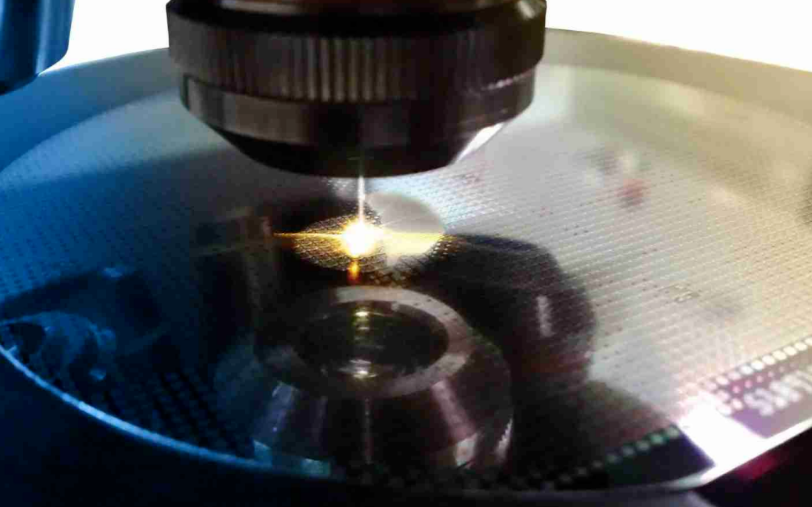
දෙවනුව, වේෆර් කැට කැපීම නිෂ්පාදන කාර්යක්ෂමතාව සහ පිරිවැය පාලනය කෙරෙහි සැලකිය යුතු බලපෑමක් ඇති කරයි. නිෂ්පාදන ක්රියාවලියේ තීරණාත්මක පියවරක් ලෙස, එහි කාර්යක්ෂමතාව ඊළඟ පියවරවල ප්රගතියට සෘජුවම බලපායි. කැට කැපීමේ ක්රියාවලිය ප්රශස්ත කිරීම, ස්වයංක්රීයකරණ මට්ටම් වැඩි කිරීම සහ කැපුම් වේගය වැඩි දියුණු කිරීම මගින් සමස්ත නිෂ්පාදන කාර්යක්ෂමතාව බෙහෙවින් වැඩි දියුණු කළ හැකිය.
අනෙක් අතට, කැට කැපීමේදී ද්රව්ය නාස්තිය පිරිවැය කළමනාකරණයේ තීරණාත්මක සාධකයකි. උසස් කැට කැපීමේ තාක්ෂණයන් භාවිතා කිරීම කැපීමේ ක්රියාවලියේදී අනවශ්ය ද්රව්ය පාඩු අඩු කරනවා පමණක් නොව වේෆර් භාවිතය වැඩි කරයි, එමඟින් නිෂ්පාදන පිරිවැය අඩු කරයි.
අර්ධ සන්නායක තාක්ෂණයේ දියුණුවත් සමඟ, වේෆර් විෂ්කම්භයන් අඛණ්ඩව වැඩි වන අතර, පරිපථ ඝනත්වයන් ඒ අනුව ඉහළ යන අතර, ඩයිසිං තාක්ෂණය සඳහා ඉහළ ඉල්ලුමක් ඇති කරයි. විශාල වේෆර් සඳහා කැපුම් මාර්ග වඩාත් නිවැරදිව පාලනය කිරීම අවශ්ය වේ, විශේෂයෙන් ඉහළ ඝනත්ව පරිපථ ප්රදේශවල, සුළු අපගමනයන් පවා බහු චිප් දෝෂ සහිත විය හැකිය. මීට අමතරව, විශාල වේෆර් සඳහා වැඩි කැපුම් රේඛා සහ වඩාත් සංකීර්ණ ක්රියාවලි පියවර ඇතුළත් වන අතර, මෙම අභියෝගවලට මුහුණ දීම සඳහා ඩයිසිං තාක්ෂණයන්හි නිරවද්යතාවය, අනුකූලතාව සහ කාර්යක්ෂමතාව තවදුරටත් වැඩිදියුණු කිරීම අවශ්ය වේ.
1.3 වේෆර් ඩයිසිං ක්රියාවලිය
වේෆර් කැට සැකසීමේ ක්රියාවලියට සූදානම් කිරීමේ අදියරේ සිට අවසාන තත්ත්ව පරීක්ෂාව දක්වා සියලුම පියවර ඇතුළත් වන අතර, කැට කපාගත් චිප්ස් වල ගුණාත්මකභාවය සහ ක්රියාකාරිත්වය සහතික කිරීම සඳහා සෑම අදියරක්ම ඉතා වැදගත් වේ. පහත දැක්වෙන්නේ එක් එක් අදියර පිළිබඳ සවිස්තරාත්මක පැහැදිලි කිරීමකි.
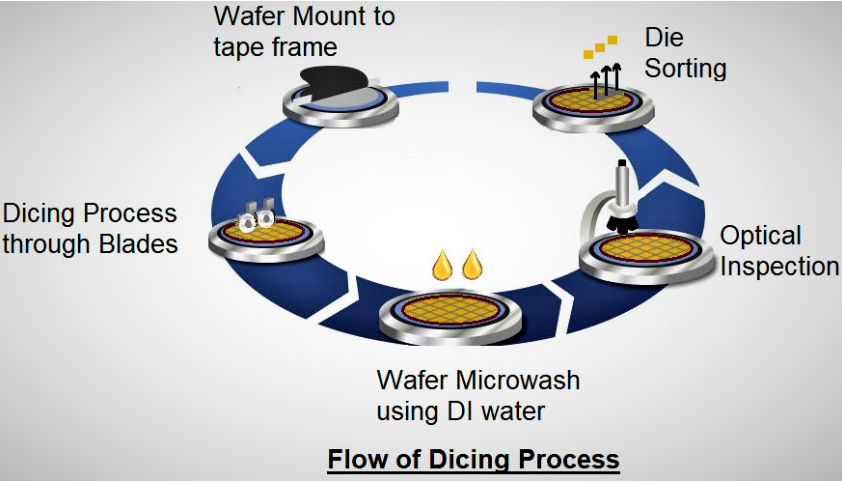
අදියර | විස්තරාත්මක විස්තරය |
සූදානම් වීමේ අදියර | -වේෆර් පිරිසිදු කිරීම: පිරිසිදු මතුපිටක් සහතික කිරීම සඳහා, අපිරිසිදුකම්, අංශු සහ අපවිත්ර ද්රව්ය ඉවත් කිරීම සඳහා, අතිධ්වනික හෝ යාන්ත්රික ස්ක්රබ් කිරීම සමඟ ඒකාබද්ධව, ඉහළ සංශුද්ධතාවයකින් යුත් ජලය සහ විශේෂිත පිරිසිදු කිරීමේ කාරක භාවිතා කරන්න. -නිරවද්ය ස්ථානගත කිරීම: නිර්මාණය කරන ලද කැපුම් මාර්ග ඔස්සේ වේෆරය නිවැරදිව බෙදී ඇති බව සහතික කිරීම සඳහා ඉහළ නිරවද්ය උපකරණ භාවිතා කරන්න. -වේෆර් සවි කිරීම: කැපීමේදී ස්ථායිතාව පවත්වා ගැනීම සඳහා, කම්පනයෙන් හෝ චලනයෙන් සිදුවන හානිය වළක්වා ගැනීම සඳහා වේෆරය ටේප් රාමුවකට සුරක්ෂිත කරන්න. |
කැපුම් අදියර | -තල ඩයිසිං: භෞතික කැපීම සඳහා අධිවේගී භ්රමණය වන දියමන්ති ආලේපිත තල භාවිතා කරන්න, සිලිකන් පාදක ද්රව්ය සඳහා සුදුසු සහ ලාභදායී. -ලේසර් ඩයිසිං: ස්පර්ශ නොවන කැපීම සඳහා අධි ශක්ති ලේසර් කිරණ භාවිතා කරන්න, ගැලියම් නයිට්රයිඩ් වැනි බිඳෙනසුලු හෝ ඉහළ දෘඪතාවක් ඇති ද්රව්ය සඳහා වඩාත් සුදුසුය, ඉහළ නිරවද්යතාවයක් සහ අඩු ද්රව්ය අලාභයක් ලබා දෙයි. -නව තාක්ෂණයන්: තාප බලපෑමට ලක් වූ කලාප අවම කරමින් කාර්යක්ෂමතාව සහ නිරවද්යතාවය තවදුරටත් වැඩිදියුණු කිරීම සඳහා ලේසර් සහ ප්ලාස්මා කැපුම් තාක්ෂණයන් හඳුන්වා දීම. |
පිරිසිදු කිරීමේ අදියර | - කැපීමේදී ජනනය වන සුන්බුන් සහ දූවිලි ඉවත් කිරීම සඳහා, පසුකාලීන ක්රියාවලීන්ට හෝ චිප විද්යුත් ක්රියාකාරිත්වයට බලපෑම් කිරීමෙන් අපද්රව්ය වැළැක්වීම සඳහා, අතිධ්වනික හෝ ඉසින පිරිසිදු කිරීම සමඟ ඒකාබද්ධව, අයනීකරණය කළ ජලය (DI ජලය) සහ විශේෂිත පිරිසිදු කිරීමේ කාරක භාවිතා කරන්න. - අධි-පිරිසිදු DI ජලය නව අපවිත්ර ද්රව්ය හඳුන්වා දීම වළක්වයි, පිරිසිදු වේෆර් පරිසරයක් සහතික කරයි. |
පරීක්ෂණ අදියර | -දෘශ්ය පරීක්ෂාව: දෝෂ ඉක්මනින් හඳුනා ගැනීමට, කැට කපාගත් චිප්ස් වල ඉරිතැලීම් හෝ චිපින් නොමැති බව සහතික කිරීමට, පරීක්ෂණ කාර්යක්ෂමතාව වැඩි දියුණු කිරීමට සහ මානව දෝෂ අවම කිරීමට AI ඇල්ගොරිතම සමඟ ඒකාබද්ධ වූ දෘශ්ය හඳුනාගැනීමේ පද්ධති භාවිතා කරන්න. -මාන මැනීම: චිපයේ මානයන් සැලසුම් පිරිවිතරයන්ට අනුකූලදැයි තහවුරු කරන්න. -විදුලි කාර්ය සාධන පරීක්ෂණය: තීරණාත්මක චිප් වල විද්යුත් ක්රියාකාරිත්වය ප්රමිතීන්ට අනුකූල වන බව සහතික කිරීම, පසුකාලීන යෙදුම්වල විශ්වසනීයත්වය සහතික කිරීම. |
වර්ග කිරීමේ අදියර | - ටේප් රාමුවෙන් සුදුසුකම් ලත් චිප්ස් වෙන් කිරීමට සහ කාර්ය සාධනය මත පදනම්ව ඒවා ස්වයංක්රීයව වර්ග කිරීමට රොබෝ ආයුධ හෝ රික්ත චූෂණ කෝප්ප භාවිතා කරන්න, නිරවද්යතාවය වැඩි දියුණු කරන අතරම නිෂ්පාදන කාර්යක්ෂමතාව සහ නම්යශීලී බව සහතික කරයි. |
වේෆර් කැපීමේ ක්රියාවලියට වේෆර් පිරිසිදු කිරීම, ස්ථානගත කිරීම, කැපීම, පිරිසිදු කිරීම, පරීක්ෂා කිරීම සහ වර්ග කිරීම ඇතුළත් වන අතර, සෑම පියවරක්ම තීරණාත්මක වේ. ස්වයංක්රීයකරණය, ලේසර් කැපීම සහ AI පරීක්ෂණ තාක්ෂණයන්හි දියුණුවත් සමඟ, නවීන වේෆර් කැපුම් පද්ධතිවලට ඉහළ නිරවද්යතාවයක්, වේගයක් සහ අඩු ද්රව්ය අලාභයක් ලබා ගත හැකිය. අනාගතයේ දී, ලේසර් සහ ප්ලාස්මා වැනි නව කැපුම් තාක්ෂණයන් ක්රමයෙන් සාම්ප්රදායික තල කැපීම ප්රතිස්ථාපනය කර, වැඩි වැඩියෙන් සංකීර්ණ චිප නිර්මාණවල අවශ්යතා සපුරාලනු ඇත, අර්ධ සන්නායක නිෂ්පාදන ක්රියාවලීන් සංවර්ධනය කිරීම තවදුරටත් ඉදිරියට ගෙන යනු ඇත.
වේෆර් කැපීමේ තාක්ෂණය සහ එහි මූලධර්ම
රූපයේ දැක්වෙන්නේ පොදු වේෆර් කැපීමේ තාක්ෂණයන් තුනක්:තල ඩයිසිං,ලේසර් ඩයිසිං, සහප්ලාස්මා ඩයිසිංමෙම ශිල්පීය ක්රම තුන පිළිබඳ සවිස්තරාත්මක විශ්ලේෂණයක් සහ අතිරේක පැහැදිලි කිරීමක් පහත දැක්වේ:
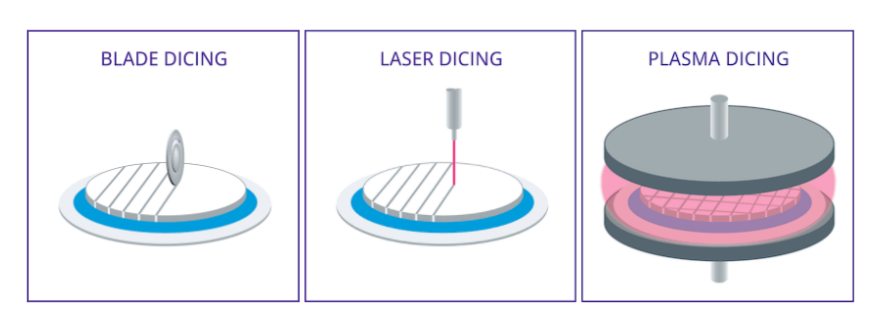
අර්ධ සන්නායක නිෂ්පාදනයේදී, වේෆර් කැපීම යනු වේෆරයේ ඝණකම මත පදනම්ව සුදුසු කැපුම් ක්රමය තෝරා ගැනීම අවශ්ය වන තීරණාත්මක පියවරකි. පළමු පියවර වන්නේ වේෆරයේ ඝණකම තීරණය කිරීමයි. වේෆර් ඝණකම මයික්රෝන 100 ඉක්මවන්නේ නම්, කැපුම් ක්රමය ලෙස තල කැට කැපීම තෝරා ගත හැකිය. තල කැට කැපීම සුදුසු නොවේ නම්, ඡේදක කැට කැපීම සහ තල කැට කැපීමේ ශිල්පීය ක්රම දෙකම ඇතුළත් අස්ථි කැට කැපීමේ ක්රමය භාවිතා කළ හැකිය.
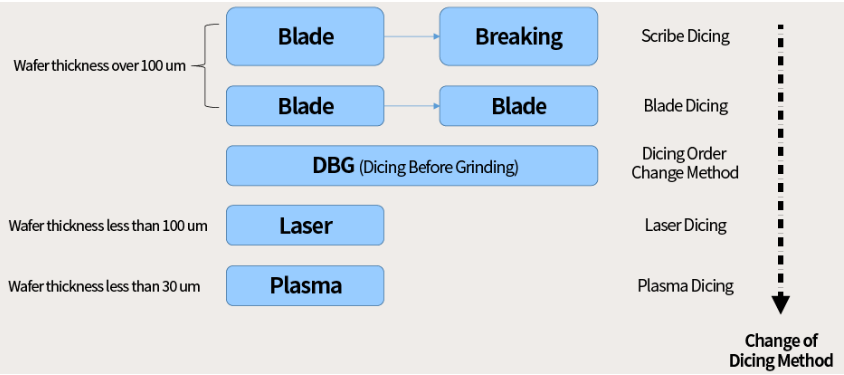
වේෆර් ඝණකම මයික්රෝන 30 ත් 100 ත් අතර වන විට, DBG (ඇඹරීමට පෙර දාදු කැට) ක්රමය නිර්දේශ කෙරේ. මෙම අවස්ථාවේ දී, හොඳම ප්රතිඵල ලබා ගැනීම සඳහා ලියන්නන් කැපීම, තල කැට කැපීම හෝ අවශ්ය පරිදි කැපුම් අනුපිළිවෙල සකස් කිරීම තෝරා ගත හැකිය.
මයික්රෝන 30 ට අඩු ඝනකමකින් යුත් අතිශය තුනී වේෆර් සඳහා, අධික හානියක් සිදු නොකර තුනී වේෆර් හරියටම කැපීමේ හැකියාව නිසා ලේසර් කැපීම වඩාත් කැමති ක්රමය බවට පත්වේ. ලේසර් කැපීම නිශ්චිත අවශ්යතා සපුරාලිය නොහැකි නම්, ප්ලාස්මා කැපීම විකල්පයක් ලෙස භාවිතා කළ හැකිය. විවිධ ඝනකම් තත්වයන් යටතේ වඩාත් සුදුසු වේෆර් කැපීමේ තාක්ෂණය තෝරා ගැනීම සහතික කිරීම සඳහා මෙම ගැලීම් සටහන පැහැදිලි තීරණ ගැනීමේ මාර්ගයක් සපයයි.
2.1 යාන්ත්රික කැපුම් තාක්ෂණය
යාන්ත්රික කැපුම් තාක්ෂණය වේෆර් කැට කැපීමේ සාම්ප්රදායික ක්රමයයි. මූලික මූලධර්මය වන්නේ වේෆර් පෙති කැපීම සඳහා කැපුම් මෙවලමක් ලෙස අධිවේගී භ්රමණය වන දියමන්ති ඇඹරුම් රෝදයක් භාවිතා කිරීමයි. ප්රධාන උපකරණවලට වායු දරණ ස්පින්ඩලයක් ඇතුළත් වන අතර එමඟින් දියමන්ති ඇඹරුම් රෝද මෙවලම ඉහළ වේගයකින් ධාවනය කර නිශ්චිත කැපීම හෝ කට්ට කිරීම සිදු කරයි. මෙම තාක්ෂණය එහි අඩු පිරිවැය, ඉහළ කාර්යක්ෂමතාව සහ පුළුල් අදාළත්වය හේතුවෙන් කර්මාන්තයේ බහුලව භාවිතා වේ.
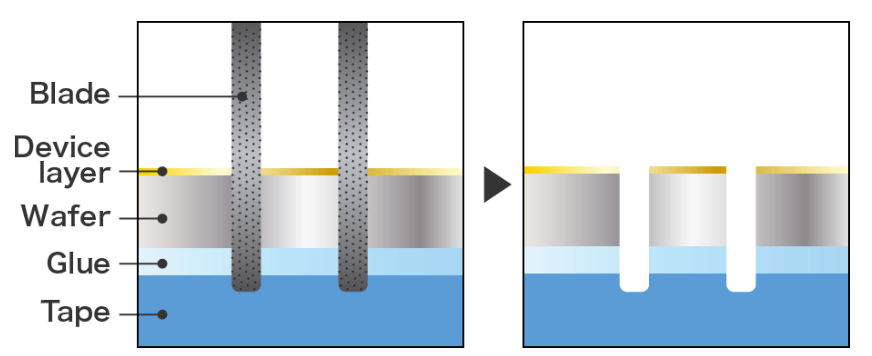
වාසි
දියමන්ති ඇඹරුම් රෝද මෙවලම්වල ඉහළ දෘඪතාව සහ ඇඳුම් ප්රතිරෝධය, සාම්ප්රදායික සිලිකන් පාදක ද්රව්ය හෝ නව සංයෝග අර්ධ සන්නායක වේවා, විවිධ වේෆර් ද්රව්යවල කැපුම් අවශ්යතාවලට අනුවර්තනය වීමට යාන්ත්රික කැපුම් තාක්ෂණයට හැකියාව ලබා දෙයි. එහි ක්රියාකාරිත්වය සරලයි, සාපේක්ෂව අඩු තාක්ෂණික අවශ්යතා සහිතව, මහා පරිමාණ නිෂ්පාදනයේ එහි ජනප්රියතාවය තවදුරටත් ප්රවර්ධනය කරයි. මීට අමතරව, ලේසර් කැපීම වැනි අනෙකුත් කැපුම් ක්රම හා සසඳන විට, යාන්ත්රික කැපීම පාලනය කළ හැකි පිරිවැයක් ඇති අතර, එය ඉහළ පරිමාවකින් යුත් නිෂ්පාදන අවශ්යතා සඳහා සුදුසු වේ.
සීමාවන්
එහි බොහෝ වාසි තිබියදීත්, යාන්ත්රික කැපුම් තාක්ෂණයට ද සීමාවන් ඇත. පළමුව, මෙවලම සහ වේෆරය අතර භෞතික සම්බන්ධතාවය හේතුවෙන්, කැපුම් නිරවද්යතාවය සාපේක්ෂව සීමිත වන අතර, බොහෝ විට පසුකාලීන චිප් ඇසුරුම් සහ පරීක්ෂණවල නිරවද්යතාවයට බලපෑ හැකි මාන අපගමනයන්ට මග පාදයි. දෙවනුව, යාන්ත්රික කැපුම් ක්රියාවලියේදී චිපින් සහ ඉරිතැලීම් වැනි දෝෂ පහසුවෙන් සිදුවිය හැකි අතර, එය අස්වැන්න අනුපාතයට බලපානවා පමණක් නොව, චිප්ස් වල විශ්වසනීයත්වය සහ ආයු කාලය කෙරෙහි ද අහිතකර ලෙස බලපෑ හැකිය. යාන්ත්රික ආතතියෙන් ඇතිවන හානිය විශේෂයෙන් ඉහළ ඝනත්ව චිප් නිෂ්පාදනය සඳහා අහිතකර වේ, විශේෂයෙන් මෙම ගැටළු වඩාත් කැපී පෙනෙන බිඳෙන සුළු ද්රව්ය කැපීමේදී.
තාක්ෂණික වැඩිදියුණු කිරීම්
මෙම සීමාවන් මඟහරවා ගැනීම සඳහා, පර්යේෂකයන් අඛණ්ඩව යාන්ත්රික කැපුම් ක්රියාවලිය ප්රශස්තකරණය කරමින් සිටී. කැපුම් නිරවද්යතාවය සහ කල්පැවැත්ම වැඩි දියුණු කිරීම සඳහා ඇඹරුම් රෝදවල සැලසුම සහ ද්රව්ය තෝරා ගැනීම වැඩි දියුණු කිරීම ප්රධාන වැඩිදියුණු කිරීම් අතර වේ. මීට අමතරව, කැපුම් උපකරණවල ව්යුහාත්මක සැලසුම් සහ පාලන පද්ධති ප්රශස්ත කිරීම කැපුම් ක්රියාවලියේ ස්ථායිතාව සහ ස්වයංක්රීයකරණය තවදුරටත් වැඩිදියුණු කර ඇත. මෙම දියුණුව මිනිස් මෙහෙයුම් නිසා ඇතිවන දෝෂ අඩු කරන අතර කැපුම්වල අනුකූලතාව වැඩි දියුණු කරයි. කැපුම් ක්රියාවලියේදී විෂමතා තත්ය කාලීනව නිරීක්ෂණය කිරීම සඳහා උසස් පරීක්ෂණ සහ තත්ත්ව පාලන තාක්ෂණයන් හඳුන්වාදීම කැපුම් විශ්වසනීයත්වය සහ අස්වැන්න සැලකිය යුතු ලෙස වැඩිදියුණු කර ඇත.
අනාගත සංවර්ධනය සහ නව තාක්ෂණයන්
යාන්ත්රික කැපුම් තාක්ෂණය තවමත් වේෆර් කැපීමේදී සැලකිය යුතු ස්ථානයක් හිමි කරගෙන ඇතත්, අර්ධ සන්නායක ක්රියාවලීන් පරිණාමය වන විට නව කැපුම් තාක්ෂණයන් වේගයෙන් ඉදිරියට යමින් පවතී. උදාහරණයක් ලෙස, තාප ලේසර් කැපුම් තාක්ෂණයේ යෙදීම යාන්ත්රික කැපීමේදී නිරවද්යතාවය සහ දෝෂ ගැටළු සඳහා නව විසඳුම් සපයයි. මෙම ස්පර්ශ නොවන කැපුම් ක්රමය වේෆර් මත භෞතික ආතතිය අඩු කරයි, විශේෂයෙන් වඩාත් බිඳෙන සුළු ද්රව්ය කැපීමේදී චිපින් සහ ඉරිතැලීම් ඇතිවීමේ සම්භාවිතාව සැලකිය යුතු ලෙස අඩු කරයි. අනාගතයේදී, නැගී එන කැපුම් ශිල්පීය ක්රම සමඟ යාන්ත්රික කැපුම් තාක්ෂණය ඒකාබද්ධ කිරීම අර්ධ සන්නායක නිෂ්පාදනයට වැඩි විකල්ප සහ නම්යශීලී බවක් ලබා දෙන අතර නිෂ්පාදන කාර්යක්ෂමතාව සහ චිපයේ ගුණාත්මකභාවය තවදුරටත් වැඩි දියුණු කරයි.
නිගමනයක් ලෙස, යාන්ත්රික කැපුම් තාක්ෂණයට යම් යම් අඩුපාඩු තිබුණද, අඛණ්ඩ තාක්ෂණික වැඩිදියුණු කිරීම් සහ නව කැපුම් ශිල්පීය ක්රම සමඟ එහි ඒකාබද්ධතාවය අර්ධ සන්නායක නිෂ්පාදනයේ වැදගත් කාර්යභාරයක් ඉටු කිරීමට සහ අනාගත ක්රියාවලීන්හි එහි තරඟකාරිත්වය පවත්වා ගැනීමට ඉඩ සලසයි.
2.2 ලේසර් කැපුම් තාක්ෂණය
වේෆර් කැපීමේ නව ක්රමයක් ලෙස ලේසර් කැපුම් තාක්ෂණය, එහි ඉහළ නිරවද්යතාවය, යාන්ත්රික සම්බන්ධතා හානි නොමැතිකම සහ වේගවත් කැපුම් හැකියාවන් හේතුවෙන් අර්ධ සන්නායක කර්මාන්තය තුළ ක්රමයෙන් පුළුල් අවධානයක් දිනා ගෙන ඇත. මෙම තාක්ෂණය වේෆර් ද්රව්යයේ මතුපිට කුඩා තාප බලපෑමට ලක් වූ කලාපයක් නිර්මාණය කිරීම සඳහා ලේසර් කදම්භයක ඉහළ ශක්ති ඝනත්වය සහ අවධානය යොමු කිරීමේ හැකියාව භාවිතා කරයි. ලේසර් කදම්භය වේෆර් එකට යොදන විට, ජනනය වන තාප ආතතිය නිසා ද්රව්යය නියමිත ස්ථානයේ කැඩී යාම සිදු වන අතර, නිරවද්ය කැපීමක් ලබා ගනී.
ලේසර් කැපුම් තාක්ෂණයේ වාසි
• ඉහළ නිරවද්යතාවය: ලේසර් කදම්භයේ නිරවද්ය ස්ථානගත කිරීමේ හැකියාව මයික්රෝන හෝ නැනෝමීටර මට්ටමේ කැපුම් නිරවද්යතාවයකට ඉඩ සලසයි, නවීන ඉහළ නිරවද්යතාවයකින් යුත්, ඉහළ ඝනත්ව ඒකාබද්ධ පරිපථ නිෂ්පාදනයේ අවශ්යතා සපුරාලයි.
• යාන්ත්රික ස්පර්ශයක් නැත: ලේසර් කැපීම වේෆරය සමඟ භෞතික සම්බන්ධතා වළක්වයි, චිපින් සහ ඉරිතැලීම් වැනි යාන්ත්රික කැපීමේදී පොදු ගැටළු වළක්වයි, චිප්ස් වල අස්වැන්න අනුපාතය සහ විශ්වසනීයත්වය සැලකිය යුතු ලෙස වැඩි දියුණු කරයි.
• වේගවත් කැපුම් වේගය: ලේසර් කැපීමේ අධික වේගය නිෂ්පාදන කාර්යක්ෂමතාව වැඩි කිරීමට දායක වන අතර, එය මහා පරිමාණ, අධිවේගී නිෂ්පාදන අවස්ථා සඳහා විශේෂයෙන් සුදුසු වේ.
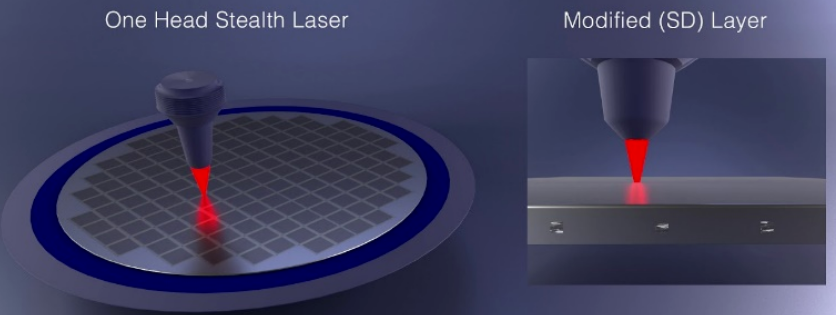
මුහුණ දුන් අභියෝග
• ඉහළ උපකරණ පිරිවැය: ලේසර් කැපුම් උපකරණ සඳහා මූලික ආයෝජනය ඉහළ මට්ටමක පවතින අතර, එය විශේෂයෙන් කුඩා හා මධ්යම ප්රමාණයේ නිෂ්පාදන ව්යවසායන් සඳහා ආර්ථික පීඩනයක් ඇති කරයි.
• සංකීර්ණ ක්රියාවලි පාලනය: ලේසර් කැපීම සඳහා ශක්ති ඝනත්වය, නාභිගත ස්ථානය සහ කැපුම් වේගය ඇතුළු පරාමිතීන් කිහිපයක නිරවද්ය පාලනය අවශ්ය වන අතර එමඟින් ක්රියාවලිය සංකීර්ණ වේ.
• තාප බලපෑමට ලක් වූ කලාප ගැටළු: ලේසර් කැපීමේ ස්පර්ශ නොවන ස්වභාවය යාන්ත්රික හානි අඩු කළද, තාප බලපෑමට ලක් වූ කලාපය (HAZ) නිසා ඇතිවන තාප ආතතිය වේෆර් ද්රව්යයේ ගුණාංගවලට අහිතකර ලෙස බලපෑ හැකිය. මෙම බලපෑම අවම කිරීම සඳහා ක්රියාවලිය තවදුරටත් ප්රශස්තිකරණය කිරීම අවශ්ය වේ.
තාක්ෂණික වැඩිදියුණු කිරීමේ උපදෙස්
මෙම අභියෝගවලට මුහුණ දීම සඳහා, පර්යේෂකයන් උපකරණ පිරිවැය අඩු කිරීම, කප්පාදු කාර්යක්ෂමතාව වැඩි දියුණු කිරීම සහ ක්රියාවලි ප්රවාහය ප්රශස්ත කිරීම කෙරෙහි අවධානය යොමු කරයි.
• කාර්යක්ෂම ලේසර් සහ දෘශ්ය පද්ධති: වඩාත් කාර්යක්ෂම ලේසර් සහ උසස් දෘශ්ය පද්ධති සංවර්ධනය කිරීමෙන්, කැපුම් නිරවද්යතාවය සහ වේගය වැඩි දියුණු කරන අතරම උපකරණ පිරිවැය අඩු කිරීමට හැකි වේ.
• ක්රියාවලි පරාමිතීන් ප්රශස්ත කිරීම: තාප බලපෑමට ලක් වූ කලාපය අඩු කරන ක්රියාවලීන් වැඩිදියුණු කිරීම සඳහා ලේසර් සහ වේෆර් ද්රව්ය අතර අන්තර්ක්රියා පිළිබඳ ගැඹුරු පර්යේෂණ සිදු කරනු ලබන අතර එමඟින් කැපුම් ගුණාත්මකභාවය වැඩි දියුණු වේ.
• බුද්ධිමත් පාලන පද්ධති: බුද්ධිමත් පාලන තාක්ෂණයන් සංවර්ධනය කිරීම ලේසර් කැපුම් ක්රියාවලිය ස්වයංක්රීය කිරීම සහ ප්රශස්ත කිරීම, එහි ස්ථායිතාව සහ අනුකූලතාව වැඩි දියුණු කිරීම අරමුණු කරයි.
ලේසර් කැපුම් තාක්ෂණය අතිශය තුනී වේෆර් සහ ඉහළ නිරවද්යතාවයකින් යුත් කැපුම් අවස්ථා වලදී විශේෂයෙන් ඵලදායී වේ. වේෆර් ප්රමාණයන් වැඩි වන විට සහ පරිපථ ඝනත්වයන් ඉහළ යන විට, සාම්ප්රදායික යාන්ත්රික කැපුම් ක්රම නවීන අර්ධ සන්නායක නිෂ්පාදනයේ ඉහළ නිරවද්යතාවය සහ ඉහළ කාර්යක්ෂමතා ඉල්ලීම් සපුරාලීමට අරගල කරයි. එහි අද්විතීය වාසි නිසා, ලේසර් කැපීම මෙම ක්ෂේත්රවල වඩාත් කැමති විසඳුම බවට පත්වෙමින් තිබේ.
ලේසර් කැපුම් තාක්ෂණය තවමත් ඉහළ උපකරණ පිරිවැය සහ ක්රියාවලි සංකීර්ණත්වය වැනි අභියෝගවලට මුහුණ දුන්නද, ඉහළ නිරවද්යතාවය සහ ස්පර්ශ නොවන හානිවල එහි අද්විතීය වාසි අර්ධ සන්නායක නිෂ්පාදනයේ සංවර්ධනය සඳහා වැදගත් දිශාවක් බවට පත් කරයි. ලේසර් තාක්ෂණය සහ බුද්ධිමත් පාලන පද්ධති අඛණ්ඩව ඉදිරියට යන විට, ලේසර් කැපීම අර්ධ සන්නායක කර්මාන්තයේ අඛණ්ඩ සංවර්ධනයට මඟ පාදන වේෆර් කැපුම් කාර්යක්ෂමතාව සහ ගුණාත්මකභාවය තවදුරටත් වැඩිදියුණු කරනු ඇතැයි අපේක්ෂා කෙරේ.
2.3 ප්ලාස්මා කැපුම් තාක්ෂණය
නැගී එන වේෆර් ඩයිසිං ක්රමයක් ලෙස ප්ලාස්මා කැපුම් තාක්ෂණය මෑත වසරවලදී සැලකිය යුතු අවධානයක් දිනාගෙන ඇත. මෙම තාක්ෂණය අධි ශක්ති ප්ලාස්මා කදම්භ භාවිතා කරමින් ප්ලාස්මා කදම්භයේ ශක්තිය, වේගය සහ කැපුම් මාර්ගය පාලනය කිරීමෙන් වේෆර් නිවැරදිව කපා, ප්රශස්ත කැපුම් ප්රතිඵල ලබා ගනී.
වැඩ කිරීමේ මූලධර්මය සහ වාසි
ප්ලාස්මා කැපීමේ ක්රියාවලිය උපකරණ මගින් ජනනය කරන ලද ඉහළ උෂ්ණත්ව, අධි ශක්ති ප්ලාස්මා කදම්භයක් මත රඳා පවතී. මෙම කදම්භයට වේෆර් ද්රව්ය එහි ද්රවාංක හෝ වාෂ්පීකරණ ස්ථානයට ඉතා කෙටි කාලයක් තුළ රත් කළ හැකි අතර එමඟින් වේගවත් කැපීමට හැකියාව ලැබේ. සාම්ප්රදායික යාන්ත්රික හෝ ලේසර් කැපීම හා සසඳන විට, ප්ලාස්මා කැපීම වේගවත් වන අතර කුඩා තාප බලපෑමට ලක් වූ කලාපයක් නිපදවයි, කැපීමේදී ඉරිතැලීම් සහ හානි සිදුවීම ඵලදායී ලෙස අඩු කරයි.
ප්රායෝගික යෙදීම් වලදී, ප්ලාස්මා කැපුම් තාක්ෂණය සංකීර්ණ හැඩතල සහිත වේෆර් හැසිරවීමට විශේෂයෙන් දක්ෂ වේ. එහි අධි ශක්ති, වෙනස් කළ හැකි ප්ලාස්මා කදම්භයට ඉහළ නිරවද්යතාවයකින් අක්රමවත් හැඩැති වේෆර් පහසුවෙන් කපා ගත හැකිය. එබැවින්, ක්ෂුද්ර ඉලෙක්ට්රොනික නිෂ්පාදනයේදී, විශේෂයෙන් අභිරුචිකරණය කළ සහ ඉහළ මට්ටමේ චිප්ස් කුඩා කණ්ඩායම් නිෂ්පාදනයේදී, මෙම තාක්ෂණය පුළුල් භාවිතය සඳහා විශාල පොරොන්දුවක් පෙන්වයි.
අභියෝග සහ සීමාවන්
ප්ලාස්මා කැපුම් තාක්ෂණයේ බොහෝ වාසි තිබියදීත්, එය සමහර අභියෝගවලට ද මුහුණ දෙයි.
• සංකීර්ණ ක්රියාවලිය: ප්ලාස්මා කැපීමේ ක්රියාවලිය සංකීර්ණ වන අතර එය සහතික කිරීම සඳහා ඉහළ නිරවද්ය උපකරණ සහ පළපුරුදු ක්රියාකරුවන් අවශ්ය වේ.කැපීමේදී නිරවද්යතාවය සහ ස්ථාවරත්වය.
• පාරිසරික පාලනය සහ ආරක්ෂාව: ප්ලාස්මා කදම්භයේ ඉහළ උෂ්ණත්ව, අධි ශක්ති ස්වභාවය නිසා දැඩි පාරිසරික පාලනයක් සහ ආරක්ෂක පියවරයන් අවශ්ය වන අතර එමඟින් ක්රියාත්මක කිරීමේ සංකීර්ණත්වය සහ පිරිවැය වැඩි වේ.
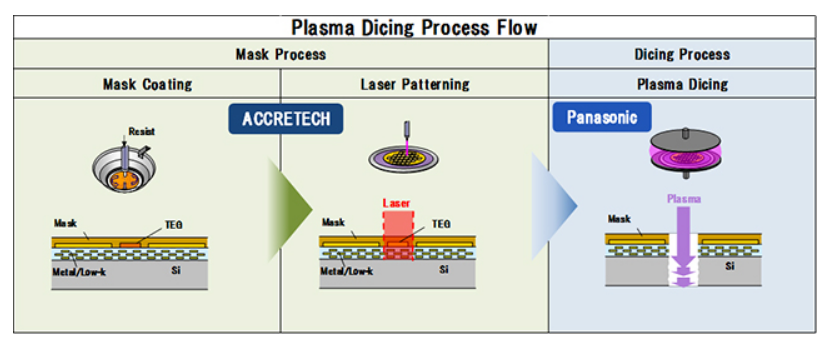
අනාගත සංවර්ධන දිශාවන්
තාක්ෂණික දියුණුවත් සමඟ, ප්ලාස්මා කැපීම හා සම්බන්ධ අභියෝග ක්රමයෙන් ජය ගැනීමට අපේක්ෂා කෙරේ. දක්ෂ හා වඩා ස්ථායී කැපුම් උපකරණ සංවර්ධනය කිරීමෙන්, අතින් මෙහෙයුම් මත යැපීම අඩු කළ හැකි අතර, එමඟින් නිෂ්පාදන කාර්යක්ෂමතාව වැඩි දියුණු කළ හැකිය. ඒ සමඟම, ක්රියාවලි පරාමිතීන් සහ කැපුම් පරිසරය ප්රශස්ත කිරීම ආරක්ෂිත අවදානම් සහ මෙහෙයුම් පිරිවැය අඩු කිරීමට උපකාරී වේ.
අර්ධ සන්නායක කර්මාන්තය තුළ, වේෆර් කැපීම සහ ඩයිසිං තාක්ෂණයේ නවෝත්පාදනයන් කර්මාන්තයේ සංවර්ධනය මෙහෙයවීම සඳහා ඉතා වැදගත් වේ. ඉහළ නිරවද්යතාවය, කාර්යක්ෂමතාව සහ සංකීර්ණ වේෆර් හැඩතල හැසිරවීමේ හැකියාව ඇති ප්ලාස්මා කැපුම් තාක්ෂණය මෙම ක්ෂේත්රයේ සැලකිය යුතු නව ක්රීඩකයෙකු ලෙස මතු වී තිබේ. සමහර අභියෝග ඉතිරිව තිබුණද, මෙම ගැටළු අඛණ්ඩ තාක්ෂණික නවෝත්පාදනයන් සමඟ ක්රමයෙන් විසඳනු ලබන අතර, අර්ධ සන්නායක නිෂ්පාදනයට වැඩි හැකියාවන් සහ අවස්ථා ගෙන එනු ඇත.
ප්ලාස්මා කැපුම් තාක්ෂණයේ යෙදුම් අපේක්ෂාවන් අති විශාල වන අතර, අනාගතයේදී අර්ධ සන්නායක නිෂ්පාදනයේ වඩාත් වැදගත් කාර්යභාරයක් ඉටු කරනු ඇතැයි අපේක්ෂා කෙරේ. අඛණ්ඩ තාක්ෂණික නවෝත්පාදන සහ ප්රශස්තිකරණය හරහා, ප්ලාස්මා කැපීම පවතින අභියෝගවලට මුහුණ දෙනවා පමණක් නොව, අර්ධ සන්නායක කර්මාන්තයේ වර්ධනයේ ප්රබල ධාවකයක් බවට පත්වනු ඇත.
2.4 ගුණාත්මකභාවය කැපීම සහ බලපෑම් කිරීමේ සාධක
පසුකාලීන චිප් ඇසුරුම් කිරීම, පරීක්ෂා කිරීම සහ අවසාන නිෂ්පාදනයේ සමස්ත ක්රියාකාරිත්වය සහ විශ්වසනීයත්වය සඳහා වේෆර් කැපීමේ ගුණාත්මකභාවය ඉතා වැදගත් වේ. කැපීමේදී ඇතිවන පොදු ගැටළු අතර ඉරිතැලීම්, චිපින් සහ කැපුම් අපගමනයන් ඇතුළත් වේ. මෙම ගැටළු එකට වැඩ කරන සාධක කිහිපයක් මගින් බලපායි.
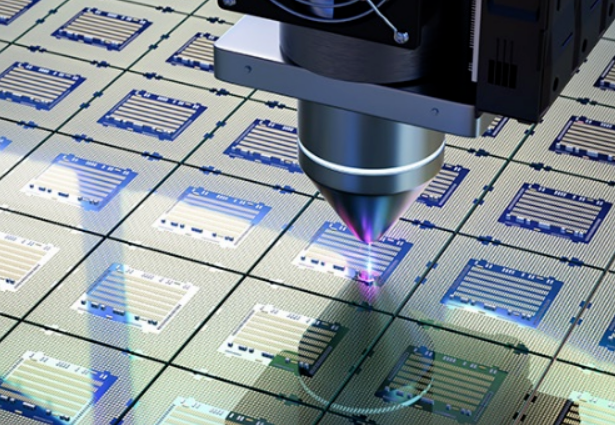
ප්රවර්ගය | අන්තර්ගතය | බලපෑම |
ක්රියාවලි පරාමිතීන් | කැපුම් වේගය, පෝෂණ අනුපාතය සහ කැපුම් ගැඹුර කැපීමේ ක්රියාවලියේ ස්ථායිතාව සහ නිරවද්යතාවයට සෘජුවම බලපායි. නුසුදුසු සැකසුම් ආතති සාන්ද්රණයට සහ අධික තාප බලපෑමට ලක් වූ කලාපයට හේතු විය හැකි අතර, එහි ප්රතිඵලයක් ලෙස ඉරිතැලීම් සහ චිපින් ඇති වේ. වේෆර් ද්රව්ය, ඝණකම සහ කැපුම් අවශ්යතා මත පදනම්ව සුදුසු පරාමිතීන් සකස් කිරීම අපේක්ෂිත කැපුම් ප්රතිඵල ලබා ගැනීම සඳහා යතුරයි. | නිවැරදි ක්රියාවලි පරාමිතීන් නිරවද්ය කැපීම සහතික කරන අතර ඉරිතැලීම් සහ චිපින් වැනි දෝෂ ඇතිවීමේ අවදානම අඩු කරයි. |
උපකරණ සහ ද්රව්ය සාධක | -තල ගුණාත්මකභාවය: තලයෙහි ද්රව්ය, දෘඪතාව සහ ඇඳීමේ ප්රතිරෝධය කැපුම් ක්රියාවලියේ සුමටතාවයට සහ කැපුම් මතුපිට සමතලාභාවයට බලපායි. දුර්වල ගුණාත්මක තල ඝර්ෂණය සහ තාප ආතතිය වැඩි කරන අතර, ඉරිතැලීම් හෝ චිපින් වලට තුඩු දිය හැකිය. නිවැරදි තල ද්රව්ය තෝරා ගැනීම ඉතා වැදගත් වේ. -සිසිලනකාරක කාර්ය සාධනය: සිසිලනකාරක කැපීමේ උෂ්ණත්වය අඩු කිරීමට, ඝර්ෂණය අවම කිරීමට සහ සුන්බුන් ඉවත් කිරීමට උපකාරී වේ. අකාර්යක්ෂම සිසිලනකාරකය ඉහළ උෂ්ණත්වයන් සහ සුන්බුන් සමුච්චය වීමට හේතු විය හැකි අතර, කැපීමේ ගුණාත්මකභාවය සහ කාර්යක්ෂමතාවයට බලපායි. කාර්යක්ෂම හා පරිසර හිතකාමී සිසිලනකාරක තෝරා ගැනීම අත්යවශ්ය වේ. | තලවල ගුණාත්මකභාවය කැපීමේ නිරවද්යතාවයට සහ සුමටතාවයට බලපායි. අකාර්යක්ෂම සිසිලනකාරකය දුර්වල කැපුම් ගුණාත්මකභාවය සහ කාර්යක්ෂමතාවයට හේතු විය හැකි අතර, ප්රශස්ත සිසිලනකාරක භාවිතයේ අවශ්යතාවය ඉස්මතු කරයි. |
ක්රියාවලි පාලනය සහ තත්ත්ව පරීක්ෂාව | -ක්රියාවලි පාලනය: කැපුම් ක්රියාවලියේ ස්ථායිතාව සහ අනුකූලතාව සහතික කිරීම සඳහා යතුරු කැපුම් පරාමිතීන් තත්ය කාලීනව නිරීක්ෂණය කිරීම සහ ගැලපීම. -තත්ත්ව පරීක්ෂාව: කැපීමෙන් පසු පෙනුම පරීක්ෂා කිරීම, මාන මිනුම් සහ විදුලි කාර්ය සාධන පරීක්ෂණ මගින් ගුණාත්මක ගැටළු හඳුනාගෙන ඉක්මනින් විසඳීමට උපකාරී වන අතර, කැපීමේ නිරවද්යතාවය සහ අනුකූලතාව වැඩි දියුණු කරයි. | නිසි ක්රියාවලි පාලනය සහ තත්ත්ව පරීක්ෂාව ස්ථාවර, උසස් තත්ත්වයේ කැපුම් ප්රතිඵල සහ විභව ගැටළු කල්තියා හඳුනා ගැනීම සහතික කිරීමට උපකාරී වේ. |

කැපුම් ගුණාත්මකභාවය වැඩි දියුණු කිරීම
කැපුම් ගුණාත්මකභාවය වැඩිදියුණු කිරීම සඳහා ක්රියාවලි පරාමිතීන්, උපකරණ සහ ද්රව්ය තෝරා ගැනීම, ක්රියාවලි පාලනය සහ පරීක්ෂාව සැලකිල්ලට ගන්නා පුළුල් ප්රවේශයක් අවශ්ය වේ. කැපුම් තාක්ෂණයන් අඛණ්ඩව පිරිපහදු කිරීමෙන් සහ ක්රියාවලි ක්රම ප්රශස්ත කිරීමෙන්, වේෆර් කැපීමේ නිරවද්යතාවය සහ ස්ථායිතාව තවදුරටත් වැඩිදියුණු කළ හැකි අතර, අර්ධ සන්නායක නිෂ්පාදන කර්මාන්තය සඳහා වඩාත් විශ්වාසදායක තාක්ෂණික සහාය ලබා දේ.
#03 කැපීමෙන් පසු හැසිරවීම සහ පරීක්ෂා කිරීම
3.1 පිරිසිදු කිරීම සහ වියළීම
වේෆර් කැපීමෙන් පසු පිරිසිදු කිරීමේ සහ වියළීමේ පියවර චිපයේ ගුණාත්මකභාවය සහ පසුකාලීන ක්රියාවලීන්හි සුමට ප්රගතිය සහතික කිරීම සඳහා ඉතා වැදගත් වේ. මෙම අදියරේදී, කැපීමේදී ජනනය වන සිලිකන් සුන්බුන්, සිසිලන අපද්රව්ය සහ අනෙකුත් දූෂක හොඳින් ඉවත් කිරීම අත්යවශ්ය වේ. පිරිසිදු කිරීමේ ක්රියාවලියේදී චිප්ස් වලට හානි නොවන බව සහතික කිරීම සහ වියළීමෙන් පසු, විඛාදනය හෝ විද්යුත් ස්ථිතික විසර්ජනය වැනි ගැටළු වළක්වා ගැනීම සඳහා චිප් මතුපිට තෙතමනයක් ඉතිරි නොවන බවට වග බලා ගැනීම ද ඒ හා සමානව වැදගත් වේ.
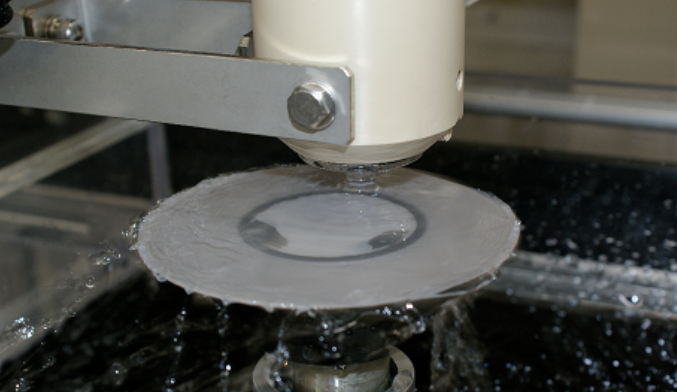
කැපීමෙන් පසු හැසිරවීම: පිරිසිදු කිරීම සහ වියළීමේ ක්රියාවලිය
ක්රියාවලි පියවර | අන්තර්ගතය | බලපෑම |
පිරිසිදු කිරීමේ ක්රියාවලිය | -ක්රමය: පිරිසිදු කිරීම සඳහා අතිධ්වනික හෝ යාන්ත්රික දත්මැදීමේ ශිල්පීය ක්රම සමඟ ඒකාබද්ධව විශේෂිත පිරිසිදු කිරීමේ කාරක සහ පිරිසිදු ජලය භාවිතා කරන්න. | අපිරිසිදු ද්රව්ය හොඳින් ඉවත් කිරීම සහතික කරන අතර පිරිසිදු කිරීමේදී චිප්ස් වලට හානි වීම වළක්වයි. |
-පිරිසිදු කිරීමේ නියෝජිත තේරීම: චිපයට හානි නොකර ඵලදායී පිරිසිදු කිරීම සහතික කිරීම සඳහා වේෆර් ද්රව්ය සහ දූෂක වර්ගය මත පදනම්ව තෝරන්න. | ඵලදායී පිරිසිදු කිරීම සහ චිප් ආරක්ෂාව සඳහා නිසි නියෝජිතයා තෝරා ගැනීම යතුරයි. | |
-පරාමිති පාලනය: නුසුදුසු පිරිසිදු කිරීම නිසා ඇතිවන ගුණාත්මක ගැටළු වළක්වා ගැනීම සඳහා පිරිසිදු කිරීමේ උෂ්ණත්වය, කාලය සහ පිරිසිදු කිරීමේ ද්රාවණ සාන්ද්රණය දැඩි ලෙස පාලනය කරන්න. | පාලනයන් වේෆරයට හානි වීම වැළැක්වීමට හෝ දූෂක ද්රව්ය ඉතිරි වීම වැළැක්වීමට උපකාරී වන අතර, එමඟින් ස්ථාවර ගුණාත්මකභාවය සහතික කෙරේ. | |
වියළීමේ ක්රියාවලිය | -සාම්ප්රදායික ක්රම: ස්වාභාවික වාතය වියළීම සහ උණුසුම් වාතය වියළීම, අඩු කාර්යක්ෂමතාවයක් ඇති අතර ස්ථිතික විදුලිය ගොඩනැගීමට හේතු විය හැක. | වියළීමේ කාලය මන්දගාමී වීම සහ ස්ථිතික ගැටළු ඇති විය හැක. |
-නවීන තාක්ෂණයන්: චිප්ස් ඉක්මනින් වියළී යාම සහ හානිකර බලපෑම් වළක්වා ගැනීම සඳහා රික්ත වියළීම සහ අධෝරක්ත වියළීම වැනි දියුණු තාක්ෂණයන් භාවිතා කරන්න. | වේගවත් හා කාර්යක්ෂම වියළීමේ ක්රියාවලියක්, ස්ථිතික විසර්ජන අවදානම හෝ තෙතමනය ආශ්රිත ගැටළු අඩු කරයි. | |
උපකරණ තෝරා ගැනීම සහ නඩත්තුව | -උපකරණ තෝරා ගැනීම: ඉහළ කාර්යසාධනයක් සහිත පිරිසිදු කිරීමේ සහ වියළන යන්ත්ර සැකසුම් කාර්යක්ෂමතාව වැඩි දියුණු කරන අතර හැසිරවීමේදී ඇති විය හැකි ගැටළු සියුම් ලෙස පාලනය කරයි. | උසස් තත්ත්වයේ යන්ත්ර මඟින් වඩා හොඳ සැකසුම් සහතික කරන අතර පිරිසිදු කිරීමේදී සහ වියළීමේදී දෝෂ ඇතිවීමේ සම්භාවිතාව අඩු කරයි. |
-උපකරණ නඩත්තුව: උපකරණ නිතිපතා පරීක්ෂා කිරීම සහ නඩත්තු කිරීම මඟින් එය ප්රශස්ත ක්රියාකාරී තත්ත්වයක පවතින බව සහතික කරන අතර, චිපයේ ගුණාත්මකභාවය සහතික කෙරේ. | නිසි නඩත්තුව උපකරණ අසමත්වීම් වළක්වයි, විශ්වාසදායක සහ උසස් තත්ත්වයේ සැකසුම් සහතික කරයි. |
කැපීමෙන් පසු පිරිසිදු කිරීම සහ වියළීම
වේෆර් කැපීමෙන් පසු පිරිසිදු කිරීමේ සහ වියළීමේ පියවර සංකීර්ණ හා සියුම් ක්රියාවලීන් වන අතර අවසාන සැකසුම් ප්රතිඵලය සහතික කිරීම සඳහා බහු සාධක හොඳින් සලකා බැලිය යුතුය. විද්යාත්මක ක්රම සහ දැඩි ක්රියා පටිපාටි භාවිතා කිරීමෙන්, එක් එක් චිපය ප්රශස්ත තත්ත්වයෙන් පසු ඇසුරුම්කරණ සහ පරීක්ෂණ අදියරවලට ඇතුළු වන බව සහතික කළ හැකිය.
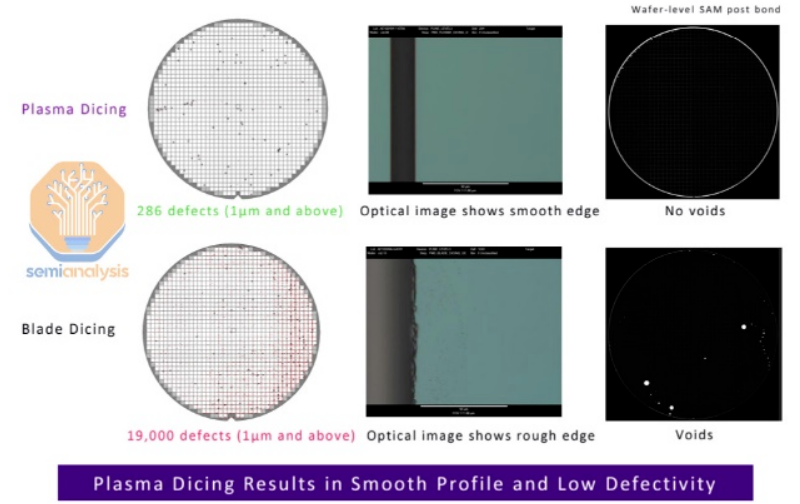
කැපීමෙන් පසු පරීක්ෂාව සහ පරීක්ෂාව
පියවර | අන්තර්ගතය | බලපෑම |
පරීක්ෂණ පියවර | 1.දෘශ්ය පරීක්ෂාව: චිප් මතුපිට ඉරිතැලීම්, චිප්ස් හෝ දූෂණය වැනි දෘශ්යමාන දෝෂ පරීක්ෂා කිරීමට දෘශ්ය හෝ ස්වයංක්රීය පරීක්ෂණ උපකරණ භාවිතා කරන්න. නාස්තිය වළක්වා ගැනීම සඳහා භෞතිකව හානි වූ චිප්ස් ඉක්මනින් හඳුනා ගන්න. | ක්රියාවලියේ මුල් අවධියේදී දෝෂ සහිත චිප්ස් හඳුනාගෙන ඉවත් කිරීමට උපකාරී වන අතර, ද්රව්යමය පාඩුව අඩු කරයි. |
2.ප්රමාණය මැනීම: චිප් මානයන් නිවැරදිව මැනීමට නිරවද්ය මිනුම් උපකරණ භාවිතා කරන්න, කැපුම් ප්රමාණය සැලසුම් පිරිවිතරයන්ට අනුකූල වන බව සහතික කිරීම සහ කාර්ය සාධන ගැටළු හෝ ඇසුරුම්කරණ දුෂ්කරතා වළක්වයි. | චිප්ස් අවශ්ය ප්රමාණයේ සීමාවන් තුළ ඇති බව සහතික කරයි, කාර්ය සාධනය පිරිහීම හෝ එකලස් කිරීමේ ගැටළු වළක්වයි. | |
3.විදුලි කාර්ය සාධන පරීක්ෂණය: අනුකූල නොවන චිප් හඳුනා ගැනීමට සහ කාර්ය සාධනයට සුදුසුකම් ලත් චිප් පමණක් ඊළඟ අදියර කරා යන බව සහතික කිරීමට, ප්රතිරෝධය, ධාරිතාව සහ ප්රේරණය වැනි ප්රධාන විද්යුත් පරාමිතීන් ඇගයීමට ලක් කරන්න. | ක්රියාවලියේදී ක්රියාකාරී සහ කාර්ය සාධනය පරීක්ෂා කරන ලද චිප් පමණක් ඉදිරියට යන බව සහතික කරයි, පසුකාලීන අවස්ථා වලදී අසාර්ථක වීමේ අවදානම අඩු කරයි. | |
පරීක්ෂණ පියවර | 1.ක්රියාකාරී පරීක්ෂාව: චිපයේ මූලික ක්රියාකාරීත්වය අපේක්ෂිත පරිදි ක්රියාත්මක වන බව තහවුරු කර ගන්න, ක්රියාකාරී අසාමාන්යතා සහිත චිප් හඳුනාගෙන ඉවත් කරන්න. | පසුකාලීන අදියර කරා යාමට පෙර චිප්ස් මූලික මෙහෙයුම් අවශ්යතා සපුරාලන බව සහතික කරයි. |
2.විශ්වසනීයත්වය පරීක්ෂා කිරීම: දිගුකාලීන භාවිතය හෝ කටුක පරිසරයන් යටතේ චිප කාර්ය සාධන ස්ථායිතාව ඇගයීමට, සාමාන්යයෙන් ඉහළ උෂ්ණත්ව වයසට යාම, අඩු උෂ්ණත්ව පරීක්ෂාව සහ සැබෑ ලෝකයේ ආන්තික තත්වයන් අනුකරණය කිරීම සඳහා ආර්ද්රතා පරීක්ෂාව ඇතුළත් වේ. | චිප්ස් විවිධ පාරිසරික තත්ත්වයන් යටතේ විශ්වාසදායක ලෙස ක්රියා කළ හැකි බව සහතික කරයි, නිෂ්පාදන කල්පැවැත්ම සහ ස්ථාවරත්වය වැඩි දියුණු කරයි. | |
3.අනුකූලතා පරීක්ෂණය: චිපය අනෙකුත් සංරචක හෝ පද්ධති සමඟ නිසි ලෙස ක්රියා කරන බව තහවුරු කර ගන්න, නොගැලපීම හේතුවෙන් කිසිදු දෝෂයක් හෝ කාර්ය සාධන පිරිහීමක් නොමැති බව සහතික කර ගන්න. | අනුකූලතා ගැටළු වළක්වා ගැනීමෙන් සැබෑ ලෝකයේ යෙදුම්වල සුමට ක්රියාකාරිත්වය සහතික කරයි. |
3.3 ඇසුරුම් කිරීම සහ ගබඩා කිරීම
වේෆර් කැපීමෙන් පසු, චිප්ස් අර්ධ සන්නායක නිෂ්පාදන ක්රියාවලියේ තීරණාත්මක ප්රතිදානයක් වන අතර, ඒවායේ ඇසුරුම් සහ ගබඩා කිරීමේ අවධීන් ද එකසේ වැදගත් වේ. ප්රවාහනය සහ ගබඩා කිරීමේදී චිප්ස් වල ආරක්ෂාව සහ ස්ථායිතාව සහතික කිරීම සඳහා පමණක් නොව, පසුකාලීන නිෂ්පාදනය, පරීක්ෂා කිරීම සහ ඇසුරුම් කිරීමේ අවධීන් සඳහා ශක්තිමත් සහයෝගයක් ලබා දීම සඳහා නිසි ඇසුරුම් සහ ගබඩා පියවර අත්යවශ්ය වේ.
පරීක්ෂණ සහ පරීක්ෂණ අදියරවල සාරාංශය:
වේෆර් කැපීමෙන් පසු චිප්ස් පරීක්ෂා කිරීමේ සහ පරීක්ෂා කිරීමේ පියවර, දෘශ්ය පරීක්ෂාව, ප්රමාණය මැනීම, විද්යුත් කාර්ය සාධන පරීක්ෂාව, ක්රියාකාරී පරීක්ෂාව, විශ්වසනීයත්වය පරීක්ෂා කිරීම සහ අනුකූලතා පරීක්ෂාව ඇතුළු අංශ ගණනාවක් ආවරණය කරයි. මෙම පියවර අන්තර් සම්බන්ධිත සහ අනුපූරක වන අතර, නිෂ්පාදනවල ගුණාත්මකභාවය සහ විශ්වසනීයත්වය සහතික කිරීම සඳහා ශක්තිමත් බාධකයක් සාදයි. දැඩි පරීක්ෂණ සහ පරීක්ෂණ ක්රියා පටිපාටි හරහා, විභව ගැටළු හඳුනාගෙන ඉක්මනින් විසඳා ගත හැකි අතර, අවසාන නිෂ්පාදනය පාරිභෝගික අවශ්යතා සහ අපේක්ෂාවන් සපුරාලන බව සහතික කරයි.
පැතිකඩ | අන්තර්ගතය |
ඇසුරුම්කරණ පියවර | 1.ප්රති-ස්ථිතික: ඇසුරුම් ද්රව්යවල විශිෂ්ට ප්රති-ස්ථිතික ගුණ තිබිය යුතු අතර එමඟින් ස්ථිතික විදුලිය උපාංගවලට හානි කිරීමෙන් හෝ ඒවායේ ක්රියාකාරිත්වයට බලපෑම් කිරීමෙන් වළක්වයි. |
2.තෙතමනය-ප්රතිරෝධී: ඇසුරුම් ද්රව්යවල ආර්ද්රතාවය නිසා ඇතිවන විඛාදනය හා විදුලි ක්රියාකාරිත්වය පිරිහීම වැළැක්වීම සඳහා හොඳ තෙතමනය ප්රතිරෝධයක් තිබිය යුතුය. | |
3.කම්පන ආරක්ෂිත: ප්රවාහනයේදී කම්පනයෙන් සහ බලපෑමෙන් චිප්ස් ආරක්ෂා කිරීම සඳහා ඇසුරුම් ද්රව්ය ඵලදායී කම්පන අවශෝෂණයක් සැපයිය යුතුය. | |
ගබඩා පරිසරය | 1.ආර්ද්රතා පාලනය: අධික ආර්ද්රතාවය නිසා ඇතිවන තෙතමනය අවශෝෂණය සහ විඛාදනය හෝ අඩු ආර්ද්රතාවය නිසා ඇතිවන ස්ථිතික ගැටළු වැළැක්වීම සඳහා සුදුසු පරාසයක් තුළ ආර්ද්රතාවය දැඩි ලෙස පාලනය කරන්න. |
2.පිරිසිදුකම: දූවිලි හා අපද්රව්ය මගින් චිප්ස් දූෂණය වීම වළක්වා ගැනීම සඳහා පිරිසිදු ගබඩා පරිසරයක් පවත්වා ගන්න. | |
3.උෂ්ණත්ව පාලනය: අඩු උෂ්ණත්වයන් නිසා ඇතිවන අධික තාපය හෝ ඝනීභවන ගැටළු හේතුවෙන් වේගවත් වයසට යාම වැළැක්වීම සඳහා සාධාරණ උෂ්ණත්ව පරාසයක් සකසා උෂ්ණත්ව ස්ථායිතාව පවත්වා ගන්න. | |
නිතිපතා පරීක්ෂාව | විභව ගැටළු කාලෝචිත ආකාරයකින් හඳුනාගෙන විසඳීම සඳහා දෘශ්ය පරීක්ෂණ, ප්රමාණ මිනුම් සහ විද්යුත් කාර්ය සාධන පරීක්ෂණ භාවිතා කරමින් ගබඩා කර ඇති චිප්ස් නිතිපතා පරීක්ෂා කර ඇගයීමට ලක් කරන්න. ගබඩා කාලය සහ කොන්දේසි මත පදනම්ව, ප්රශස්ත තත්ත්වයේ භාවිතා කරන බව සහතික කිරීම සඳහා චිප්ස් භාවිතය සැලසුම් කරන්න. |
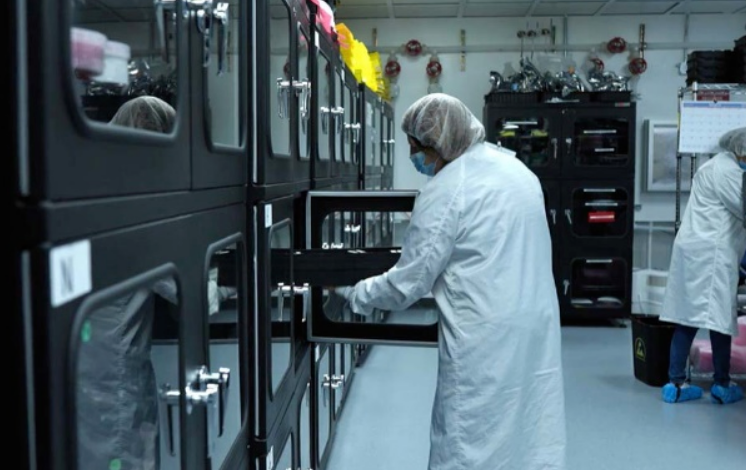
වේෆර් ඩයිසිං ක්රියාවලියේදී ක්ෂුද්ර ඉරිතැලීම් සහ හානි පිළිබඳ ගැටළුව අර්ධ සන්නායක නිෂ්පාදනයේ සැලකිය යුතු අභියෝගයකි. කැපුම් ආතතිය මෙම සංසිද්ධියට ප්රධාන හේතුව වන අතර, එය වේෆර් මතුපිට කුඩා ඉරිතැලීම් සහ හානි ඇති කරන අතර එමඟින් නිෂ්පාදන පිරිවැය වැඩි වන අතර නිෂ්පාදන ගුණාත්මකභාවය අඩු වේ.
මෙම අභියෝගයට මුහුණ දීම සඳහා, කැපුම් ආතතිය අවම කිරීම සහ ප්රශස්ත කැපුම් ශිල්පීය ක්රම, මෙවලම් සහ කොන්දේසි ක්රියාත්මක කිරීම ඉතා වැදගත් වේ. තල ද්රව්ය, කැපුම් වේගය, පීඩනය සහ සිසිලන ක්රම වැනි සාධක කෙරෙහි ප්රවේශමෙන් අවධානය යොමු කිරීම ක්ෂුද්ර ඉරිතැලීම් ඇතිවීම අඩු කිරීමට සහ ක්රියාවලියේ සමස්ත අස්වැන්න වැඩි දියුණු කිරීමට උපකාරී වේ. මීට අමතරව, ලේසර් ඩයිසිං වැනි වඩාත් දියුණු කැපුම් තාක්ෂණයන් පිළිබඳ අඛණ්ඩ පර්යේෂණ, මෙම ගැටළු තවදුරටත් අවම කිරීම සඳහා ක්රම ගවේෂණය කරයි.
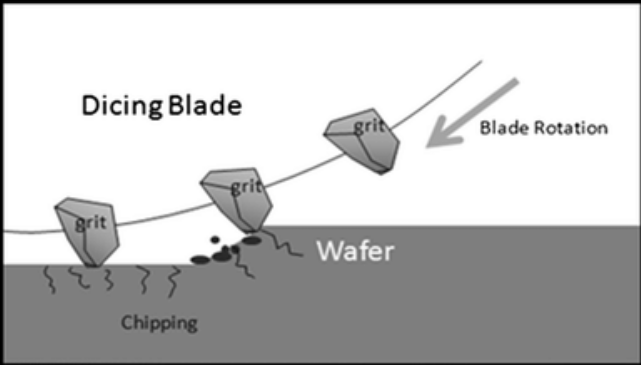
බිඳෙන සුළු ද්රව්යයක් ලෙස, වේෆර් යාන්ත්රික, තාප හෝ රසායනික ආතතියට ලක් වූ විට අභ්යන්තර ව්යුහාත්මක වෙනස්කම් වලට ගොදුරු වන අතර එමඟින් ක්ෂුද්ර ඉරිතැලීම් ඇති වේ. මෙම ඉරිතැලීම් වහාම නොපෙනී යා හැකි වුවද, නිෂ්පාදන ක්රියාවලිය ඉදිරියට යත්ම ඒවා ප්රසාරණය වී වඩාත් දරුණු හානියක් සිදු කළ හැකිය. උෂ්ණත්ව උච්චාවචනයන් සහ අතිරේක යාන්ත්රික ආතතීන් මෙම ක්ෂුද්ර ඉරිතැලීම් දෘශ්යමාන අස්ථි බිඳීම් බවට පරිණාමය වීමට හේතු විය හැකි අතර, එය චිප් අසාර්ථක වීමට හේතු විය හැක.
මෙම අවදානම අවම කිරීම සඳහා, කැපුම් වේගය, පීඩනය සහ උෂ්ණත්වය වැනි පරාමිතීන් ප්රශස්ත කිරීම මගින් කැපුම් ක්රියාවලිය ප්රවේශමෙන් පාලනය කිරීම අත්යවශ්ය වේ. ලේසර් කැට කැපීම වැනි අඩු ආක්රමණශීලී කැපුම් ක්රම භාවිතා කිරීමෙන් වේෆරය මත යාන්ත්රික ආතතිය අඩු කර ක්ෂුද්ර ඉරිතැලීම් සෑදීම අවම කළ හැකිය. මීට අමතරව, වේෆර් කැට කැපීමේ ක්රියාවලියේදී අධෝරක්ත ස්කෑනිං හෝ එක්ස් කිරණ ප්රතිබිම්භකරණය වැනි උසස් පරීක්ෂණ ක්රම ක්රියාත්මක කිරීමෙන් මෙම මුල් අවධියේ ඉරිතැලීම් තවදුරටත් හානි කිරීමට පෙර හඳුනා ගැනීමට උපකාරී වේ.
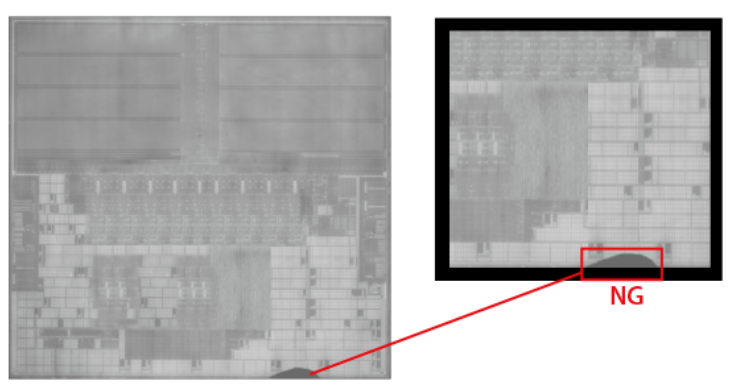
වේෆර් මතුපිටට සිදුවන හානිය ඩයිසිං ක්රියාවලියේදී සැලකිය යුතු සැලකිල්ලක් දක්වයි, මන්ද එය චිපයේ ක්රියාකාරිත්වයට සහ විශ්වසනීයත්වයට සෘජු බලපෑමක් ඇති කළ හැකිය. එවැනි හානියක් කැපුම් මෙවලම් අනිසි ලෙස භාවිතා කිරීම, වැරදි කැපුම් පරාමිතීන් හෝ වේෆරයටම ආවේණික ද්රව්ය දෝෂ නිසා සිදුවිය හැකිය. හේතුව කුමක් වුවත්, මෙම හානි පරිපථයේ විද්යුත් ප්රතිරෝධයේ හෝ ධාරිතාවයේ වෙනස්කම් වලට තුඩු දිය හැකි අතර එය සමස්ත ක්රියාකාරිත්වයට බලපායි.
මෙම ගැටළු විසඳීම සඳහා, ප්රධාන උපාය මාර්ග දෙකක් ගවේෂණය කරනු ලැබේ:
1. කැපුම් මෙවලම් සහ පරාමිතීන් ප්රශස්ත කිරීම: තියුණු තල භාවිතා කිරීමෙන්, කැපුම් වේගය සකස් කිරීමෙන් සහ කැපුම් ගැඹුර වෙනස් කිරීමෙන්, කැපුම් ක්රියාවලියේදී ආතති සාන්ද්රණය අවම කර ගත හැකි අතර එමඟින් හානි වීමේ විභවය අඩු කරයි.
2. නව කැපුම් තාක්ෂණයන් ගවේෂණය කිරීම: ලේසර් කැපීම සහ ප්ලාස්මා කැපීම වැනි උසස් ශිල්පීය ක්රම මඟින් වේෆරයට සිදුවන හානිය අවම කරන අතරම වැඩි දියුණු කළ නිරවද්යතාවයක් ලබා දෙයි. වේෆරය මත තාප හා යාන්ත්රික ආතතිය අවම කරමින් ඉහළ කැපුම් නිරවද්යතාවයක් ලබා ගැනීමට ක්රම සොයා ගැනීමට මෙම තාක්ෂණයන් අධ්යයනය කරමින් පවතී.
තාප බලපෑම් ප්රදේශය සහ කාර්ය සාධනය කෙරෙහි එහි බලපෑම්
ලේසර් සහ ප්ලාස්මා කැපීම වැනි තාප කැපුම් ක්රියාවලීන්හිදී, ඉහළ උෂ්ණත්වයන් අනිවාර්යයෙන්ම වේෆරයේ මතුපිට තාප බලපෑම් කලාපයක් නිර්මාණය කරයි. උෂ්ණත්ව අනුක්රමය සැලකිය යුතු මෙම ප්රදේශය, ද්රව්යයේ ගුණාංග වෙනස් කළ හැකි අතර, එය චිපයේ අවසාන ක්රියාකාරිත්වයට බලපායි.
තාප බලපෑමට ලක් වූ කලාපයේ (TAZ) බලපෑම:
ස්ඵටික ව්යුහයේ වෙනස්කම්: ඉහළ උෂ්ණත්ව යටතේ, වේෆර් ද්රව්ය තුළ ඇති පරමාණු නැවත සකස් විය හැකි අතර, එමඟින් ස්ඵටික ව්යුහයේ විකෘති කිරීම් ඇති වේ. මෙම විකෘතිය ද්රව්යය දුර්වල කරයි, එහි යාන්ත්රික ශක්තිය සහ ස්ථායිතාව අඩු කරයි, එමඟින් භාවිතයේදී චිප් අසාර්ථක වීමේ අවදානම වැඩි වේ.
විදුලි ගුණාංගවල වෙනස්කම්: ඉහළ උෂ්ණත්වයන් අර්ධ සන්නායක ද්රව්යවල වාහක සාන්ද්රණය සහ සංචලතාව වෙනස් කළ හැකි අතර, එය චිපයේ විද්යුත් සන්නායකතාවය සහ ධාරා සම්ප්රේෂණ කාර්යක්ෂමතාවයට බලපායි. මෙම වෙනස්කම් චිප ක්රියාකාරිත්වයේ අඩුවීමට හේතු විය හැකි අතර, එය එහි අපේක්ෂිත අරමුණට නුසුදුසු විය හැකිය.
මෙම බලපෑම් අවම කිරීම සඳහා, කැපීමේදී උෂ්ණත්වය පාලනය කිරීම, කැපුම් පරාමිතීන් ප්රශස්ත කිරීම සහ සිසිලන ජෙට් හෝ පසු සැකසුම් ප්රතිකාර වැනි ක්රම ගවේෂණය කිරීම තාප බලපෑමේ ප්රමාණය අඩු කිරීමට සහ ද්රව්ය අඛණ්ඩතාව පවත්වා ගැනීමට අත්යවශ්ය උපාය මාර්ග වේ.
සමස්තයක් වශයෙන්, ක්ෂුද්ර ඉරිතැලීම් සහ තාප බලපෑම් කලාප යන දෙකම වේෆර් ඩයිසිං තාක්ෂණයේ තීරණාත්මක අභියෝග වේ. අර්ධ සන්නායක නිෂ්පාදනවල ගුණාත්මකභාවය වැඩිදියුණු කිරීමට සහ ඒවායේ වෙළඳපල තරඟකාරිත්වය වැඩි දියුණු කිරීමට තාක්ෂණික දියුණුව සහ තත්ත්ව පාලන පියවරයන් සමඟ අඛණ්ඩ පර්යේෂණ අවශ්ය වනු ඇත.
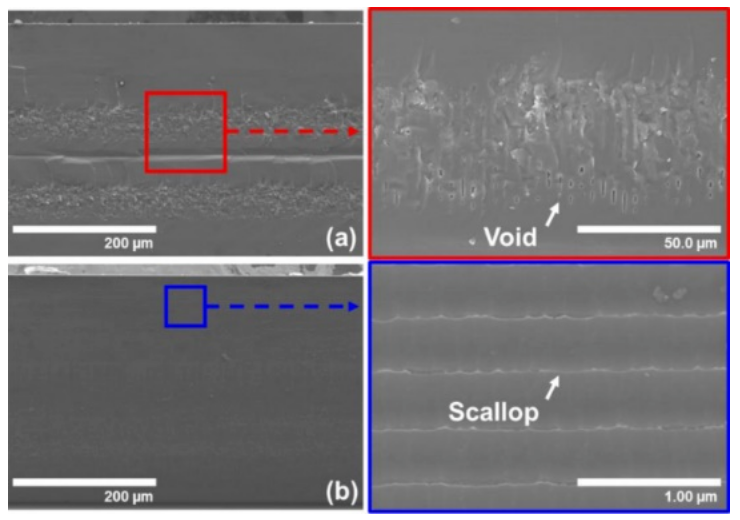
තාප බලපෑම් කලාපය පාලනය කිරීම සඳහා පියවර:
කැපුම් ක්රියාවලි පරාමිතීන් ප්රශස්ත කිරීම: කැපුම් වේගය සහ බලය අඩු කිරීමෙන් තාප බලපෑම් කලාපයේ (TAZ) ප්රමාණය ඵලදායී ලෙස අවම කළ හැකිය. මෙය වේෆරයේ ද්රව්යමය ගුණාංගවලට සෘජුවම බලපාන කැපුම් ක්රියාවලියේදී ජනනය වන තාප ප්රමාණය පාලනය කිරීමට උපකාරී වේ.
උසස් සිසිලන තාක්ෂණයන්: ද්රව නයිට්රජන් සිසිලනය සහ ක්ෂුද්ර තරල සිසිලනය වැනි තාක්ෂණයන් යෙදීමෙන් තාප බලපෑම් කලාපයේ පරාසය සැලකිය යුතු ලෙස සීමා කළ හැකිය. මෙම සිසිලන ක්රම තාපය වඩාත් කාර්යක්ෂමව විසුරුවා හැරීමට උපකාරී වන අතර එමඟින් වේෆරයේ ද්රව්යමය ගුණාංග ආරක්ෂා කර තාප හානිය අවම කරයි.
ද්රව්ය තේරීම: පර්යේෂකයන් විශිෂ්ට තාප සන්නායකතාවක් සහ යාන්ත්රික ශක්තියක් ඇති කාබන් නැනෝ ටියුබ් සහ ග්රැෆීන් වැනි නව ද්රව්ය ගවේෂණය කරමින් සිටී. මෙම ද්රව්ය චිප්ස් වල සමස්ත ක්රියාකාරිත්වය වැඩි දියුණු කරන අතරම තාප බලපෑම් කලාපය අඩු කළ හැකිය.
සාරාංශයක් ලෙස, තාප බලපෑම් කලාපය තාප කැපුම් තාක්ෂණයන්හි නොවැළැක්විය හැකි ප්රතිවිපාකයක් වුවද, ප්රශස්ත සැකසුම් ශිල්පීය ක්රම සහ ද්රව්ය තෝරා ගැනීම හරහා එය ඵලදායී ලෙස පාලනය කළ හැකිය. අනාගත පර්යේෂණ වඩාත් කාර්යක්ෂම හා නිරවද්ය වේෆර් ඩයිසිං ලබා ගැනීම සඳහා තාප කැපුම් ක්රියාවලීන් සියුම්-සුසර කිරීම සහ ස්වයංක්රීය කිරීම කෙරෙහි අවධානය යොමු කරනු ඇත.

ශේෂ උපාය මාර්ගය:
වේෆර් අස්වැන්න සහ නිෂ්පාදන කාර්යක්ෂමතාව අතර ප්රශස්ත සමතුලිතතාවය සාක්ෂාත් කර ගැනීම වේෆර් ඩයිසිං තාක්ෂණයේ අඛණ්ඩ අභියෝගයකි. තාර්කික නිෂ්පාදන උපාය මාර්ගයක් සහ ක්රියාවලි පරාමිතීන් සංවර්ධනය කිරීම සඳහා නිෂ්පාදකයින් වෙළඳපල ඉල්ලුම, නිෂ්පාදන පිරිවැය සහ නිෂ්පාදන ගුණාත්මකභාවය වැනි බහුවිධ සාධක සලකා බැලිය යුතුය. ඒ සමඟම, උසස් කැපුම් උපකරණ හඳුන්වා දීම, ක්රියාකරු කුසලතා වැඩිදියුණු කිරීම සහ අමුද්රව්ය තත්ත්ව පාලනය වැඩි දියුණු කිරීම නිෂ්පාදන කාර්යක්ෂමතාව වැඩි කරන අතරම අස්වැන්න පවත්වා ගැනීමට හෝ වැඩිදියුණු කිරීමට අත්යවශ්ය වේ.
අනාගත අභියෝග සහ අවස්ථා:
අර්ධ සන්නායක තාක්ෂණයේ දියුණුවත් සමඟ, වේෆර් කැපීම නව අභියෝග සහ අවස්ථාවන්ට මුහුණ දෙයි. චිප් ප්රමාණයන් හැකිලී ඒකාබද්ධ කිරීම වැඩි වන විට, කැපුම් නිරවද්යතාවය සහ ගුණාත්මකභාවය සඳහා වන ඉල්ලීම් සැලකිය යුතු ලෙස වර්ධනය වේ. ඒ සමඟම, නැගී එන තාක්ෂණයන් වේෆර් කැපීමේ ශිල්පීය ක්රම සංවර්ධනය සඳහා නව අදහස් සපයයි. නිෂ්පාදකයින් වෙළඳපල ගතිකත්වයන් සහ තාක්ෂණික ප්රවණතාවලට අනුගත විය යුතු අතර, වෙළඳපල වෙනස්කම් සහ තාක්ෂණික ඉල්ලීම් සපුරාලීම සඳහා නිෂ්පාදන උපාය මාර්ග සහ ක්රියාවලි පරාමිතීන් අඛණ්ඩව සකස් කර ප්රශස්ත කළ යුතුය.
අවසාන වශයෙන්, වෙළඳපල ඉල්ලුම, නිෂ්පාදන පිරිවැය සහ නිෂ්පාදන ගුණාත්මකභාවය පිළිබඳ සලකා බැලීම් ඒකාබද්ධ කිරීමෙන් සහ උසස් උපකරණ සහ තාක්ෂණය හඳුන්වා දීමෙන්, ක්රියාකරු කුසලතා වැඩි දියුණු කිරීමෙන් සහ අමුද්රව්ය පාලනය ශක්තිමත් කිරීමෙන්, නිෂ්පාදකයින්ට වේෆර් ඩයිසිං අතරතුර වේෆර් අස්වැන්න සහ නිෂ්පාදන කාර්යක්ෂමතාව අතර හොඳම සමතුලිතතාවය ලබා ගත හැකි අතර, එය කාර්යක්ෂම හා උසස් තත්ත්වයේ අර්ධ සන්නායක නිෂ්පාදන නිෂ්පාදනයකට මග පාදයි.
අනාගත දැක්ම:
වේගවත් තාක්ෂණික දියුණුවත් සමඟ, අර්ධ සන්නායක තාක්ෂණය පෙර නොවූ විරූ වේගයකින් ඉදිරියට යමින් පවතී. අර්ධ සන්නායක නිෂ්පාදනයේ තීරණාත්මක පියවරක් ලෙස, වේෆර් කැපීමේ තාක්ෂණය ආකර්ෂණීය නව වර්ධනයන් සඳහා සූදානම්ව සිටී. ඉදිරිය දෙස බලන විට, වේෆර් කැපීමේ තාක්ෂණය නිරවද්යතාවය, කාර්යක්ෂමතාව සහ පිරිවැයෙහි සැලකිය යුතු දියුණුවක් අත්කර ගනු ඇතැයි අපේක්ෂා කරන අතර, අර්ධ සන්නායක කර්මාන්තයේ අඛණ්ඩ වර්ධනයට නව ජීව ශක්තියක් එන්නත් කරයි.
නිරවද්යතාවය වැඩි කිරීම:
ඉහළ නිරවද්යතාවයක් ලුහුබැඳීමේදී, වේෆර් කැපුම් තාක්ෂණය පවතින ක්රියාවලීන්හි සීමාවන් අඛණ්ඩව තල්ලු කරනු ඇත. කැපුම් ක්රියාවලියේ භෞතික හා රසායනික යාන්ත්රණයන් ගැඹුරින් අධ්යයනය කිරීමෙන් සහ කැපුම් පරාමිතීන් නිවැරදිව පාලනය කිරීමෙන්, වඩ වඩාත් සංකීර්ණ පරිපථ සැලසුම් අවශ්යතා සපුරාලීම සඳහා සියුම් කැපුම් ප්රතිඵල ලබා ගත හැකිය. මීට අමතරව, නව ද්රව්ය සහ කැපුම් ක්රම ගවේෂණය කිරීමෙන් අස්වැන්න සහ ගුණාත්මකභාවය සැලකිය යුතු ලෙස වැඩිදියුණු වේ.
කාර්යක්ෂමතාව වැඩි දියුණු කිරීම:
නව වේෆර් කැපුම් උපකරණ ස්මාර්ට් සහ ස්වයංක්රීය නිර්මාණය කෙරෙහි අවධානය යොමු කරනු ඇත. උසස් පාලන පද්ධති සහ ඇල්ගොරිතම හඳුන්වාදීම මඟින් විවිධ ද්රව්ය හා සැලසුම් අවශ්යතා සපුරාලීම සඳහා කැපුම් පරාමිතීන් ස්වයංක්රීයව සකස් කිරීමට උපකරණවලට හැකියාව ලැබෙනු ඇති අතර එමඟින් නිෂ්පාදන කාර්යක්ෂමතාව සැලකිය යුතු ලෙස වැඩිදියුණු වේ. බහු-වේෆර් කැපුම් තාක්ෂණය සහ වේගවත් තල ප්රතිස්ථාපන පද්ධති වැනි නවෝත්පාදනයන් කාර්යක්ෂමතාව වැඩි දියුණු කිරීමේදී තීරණාත්මක කාර්යභාරයක් ඉටු කරනු ඇත.
පිරිවැය අඩු කිරීම:
වේෆර් කැපීමේ තාක්ෂණය සංවර්ධනය කිරීම සඳහා පිරිවැය අඩු කිරීම ප්රධාන දිශාවකි. නව ද්රව්ය හා කැපුම් ක්රම සංවර්ධනය වන විට, උපකරණ පිරිවැය සහ නඩත්තු වියදම් ඵලදායී ලෙස පාලනය කිරීමට අපේක්ෂා කෙරේ. මීට අමතරව, නිෂ්පාදන ක්රියාවලීන් ප්රශස්ත කිරීම සහ සීරීම් අනුපාත අඩු කිරීම නිෂ්පාදනය අතරතුර නාස්තිය තවදුරටත් අඩු කරනු ඇති අතර එමඟින් සමස්ත නිෂ්පාදන පිරිවැය අඩු වේ.
ස්මාර්ට් නිෂ්පාදනය සහ IoT:
ස්මාර්ට් නිෂ්පාදන සහ අන්තර්ජාල දේවල් (IoT) තාක්ෂණයන් ඒකාබද්ධ කිරීම වේෆර් කැපීමේ තාක්ෂණයට පරිවර්තනීය වෙනස්කම් ගෙන එනු ඇත. උපාංග අතර අන්තර් සම්බන්ධතාවය සහ දත්ත හුවමාරුව හරහා, නිෂ්පාදන ක්රියාවලියේ සෑම පියවරක්ම තත්ය කාලීනව නිරීක්ෂණය කර ප්රශස්ත කළ හැකිය. මෙය නිෂ්පාදන කාර්යක්ෂමතාව සහ නිෂ්පාදන ගුණාත්මකභාවය වැඩි දියුණු කරනවා පමණක් නොව, සමාගම්වලට වඩාත් නිවැරදි වෙළඳපල පුරෝකථනය සහ තීරණ ගැනීමේ සහාය ද සපයයි.
අනාගතයේදී, වේෆර් කැපීමේ තාක්ෂණය නිරවද්යතාවය, කාර්යක්ෂමතාව සහ පිරිවැය අතින් කැපී පෙනෙන දියුණුවක් ලබා ගනු ඇත. මෙම දියුණුව අර්ධ සන්නායක කර්මාන්තයේ අඛණ්ඩ සංවර්ධනයට හේතු වන අතර මානව සමාජයට වැඩි තාක්ෂණික නවෝත්පාදන සහ පහසුව ගෙන එනු ඇත.
පළ කිරීමේ කාලය: නොවැම්බර්-19-2024